In the construction industry, everything comes with a manual. We have standard operating procedures for different construction activities, and we need to follow them to produce the correct item. But where are standard operating procedures for quality management practices? There are many approaches listed in multiple books, but which are the ones we should adopt?
This question poses such importance as it will later define the organization's very fabric. The construction industry is adapting to significant changes by focusing on proactive problem-solving approaches. These approaches may vary, but the focus is to eliminate or reduce the imminent threat of quality loss.
These approaches tend to eliminate or reduce risk probability at its root-cause level. Even if the problem occurs, the solution can be provided easily using them. Meanwhile, using these approaches helps us utilize the opportunity to understand the root cause of the risk & adapt the system to avoid future confrontation with it. This leads to continual improvement in the system through real-time data-driven techniques.
These approaches were first adopted in the industry in a controlled environment. Adopting them in the construction industry has a different interpretation as it has a vast number of techniques & environment is not controlled. Here I have listed four approaches and how they can be applied to the construction industry.
1. Kaizen Approach:
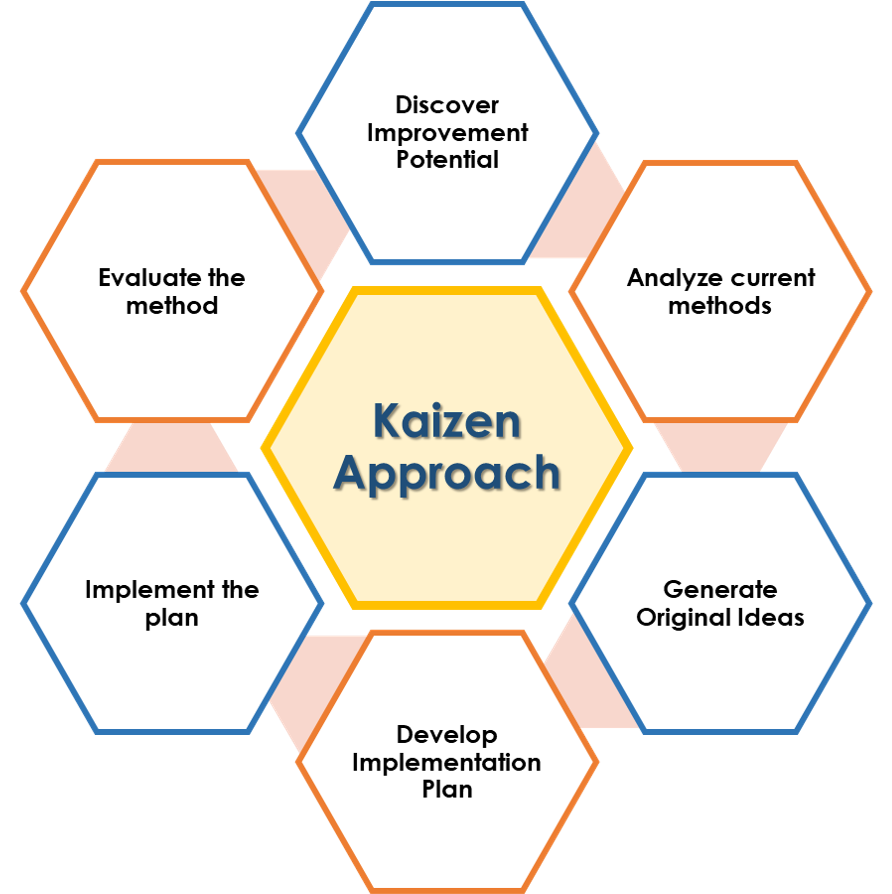
The definition of Kaizen comes from two Japanese words: 'kai' meaning 'change' and 'zen' meaning 'good'. This concept was first introduced in the 1980s by the Japanese car company, Toyota. The company aimed to develop a business model that catches errors in quality as soon as they occur.
The process focuses on continuous improvement techniques rather than strength or intelligence. The process sees the potential of improving mistakes & efforts to reduce errors in the procedures.
Kaizen is a six-step continual improvement procedure
- Discover improvement Potential
- Analyze current methods
- Generate Original Ideas
- Develop Implementation Plan
- Implement the plan
- Evaluate the new method
-
How is Kaizen used in Construction?
Since the above concept was developed for the manufacturing process in a controlled environment, it required modification when applied to Construction. Since the construction process depends on many factors such as environment, materials, the procedure followed & maintenance of the property. Thus, for Construction, Kaizen became a proactive management approach that maximizes project value and minimizes waste.
Kaizen focuses on reducing non-conformance costs. Non-conformance costs are costs that are a by-product of poor quality achieved in Construction. Kaizen method focuses on avoiding wasting resources & identifies and eliminates the root cause of the wastage by total involvement of employees of all levels.
There are many tools used in the kaizen method to improve quality & reduce cost in the construction process. These tools are discussed in detail in a further blog.
2. Six-Sigma Approach:
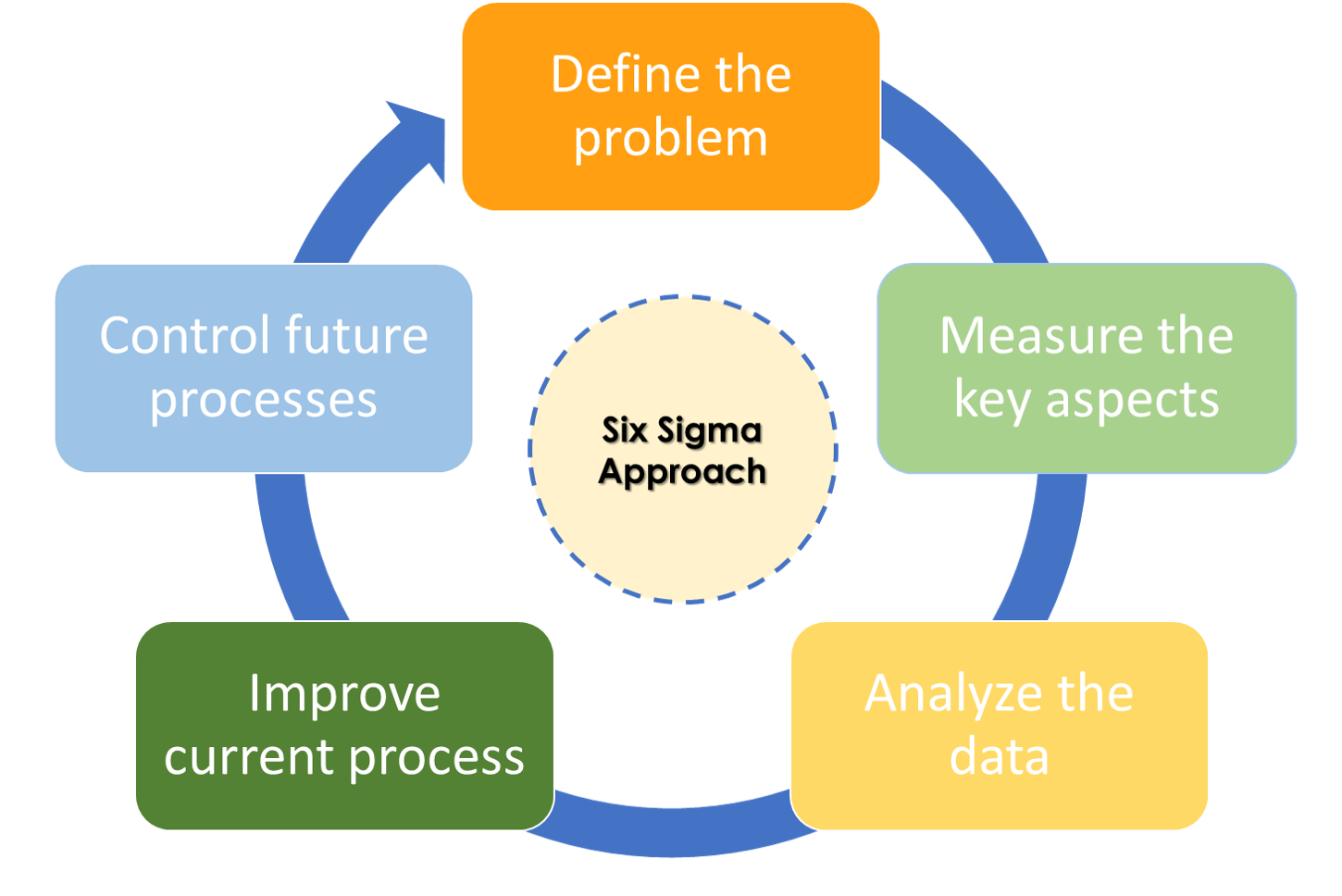
The name Six Sigma is derived from the bell curve used in statistics, where one Sigma represents one standard deviation away from the mean. It was introduced by an American engineer working for Motorola Company in 1986. Six Sigma is a measurement-based strategy for process improvement. It has followed the principle of the DMAIC Model for Quality Improvement. It is an integral part of the Six-Sigma Approach but can also be used as a stand-alone Process in quality implementation.
DMAIC Model approach is as follows:
- Define the problem
- Measure key Aspects
- Analyze the Data
- Improve current process
- Control the future process
How is Six-Sigma Process used in Construction?
Construction Project, which uses the six-sigma Approach, aim to reduce & to remove defects. Defect, by definition, does not only rework or wastage but also the inability to provide customer satisfaction. Six-Sigma's Control phase is specifically helpful to contractors & managers to strengthen their financial aspects.
The main aspect of this process is to maintain flow & manage resources like material, time, capital & manpower. This is also a continuous improvement procedure applied to achieve the highest efficiency in Construction.
3. Lean Approach:
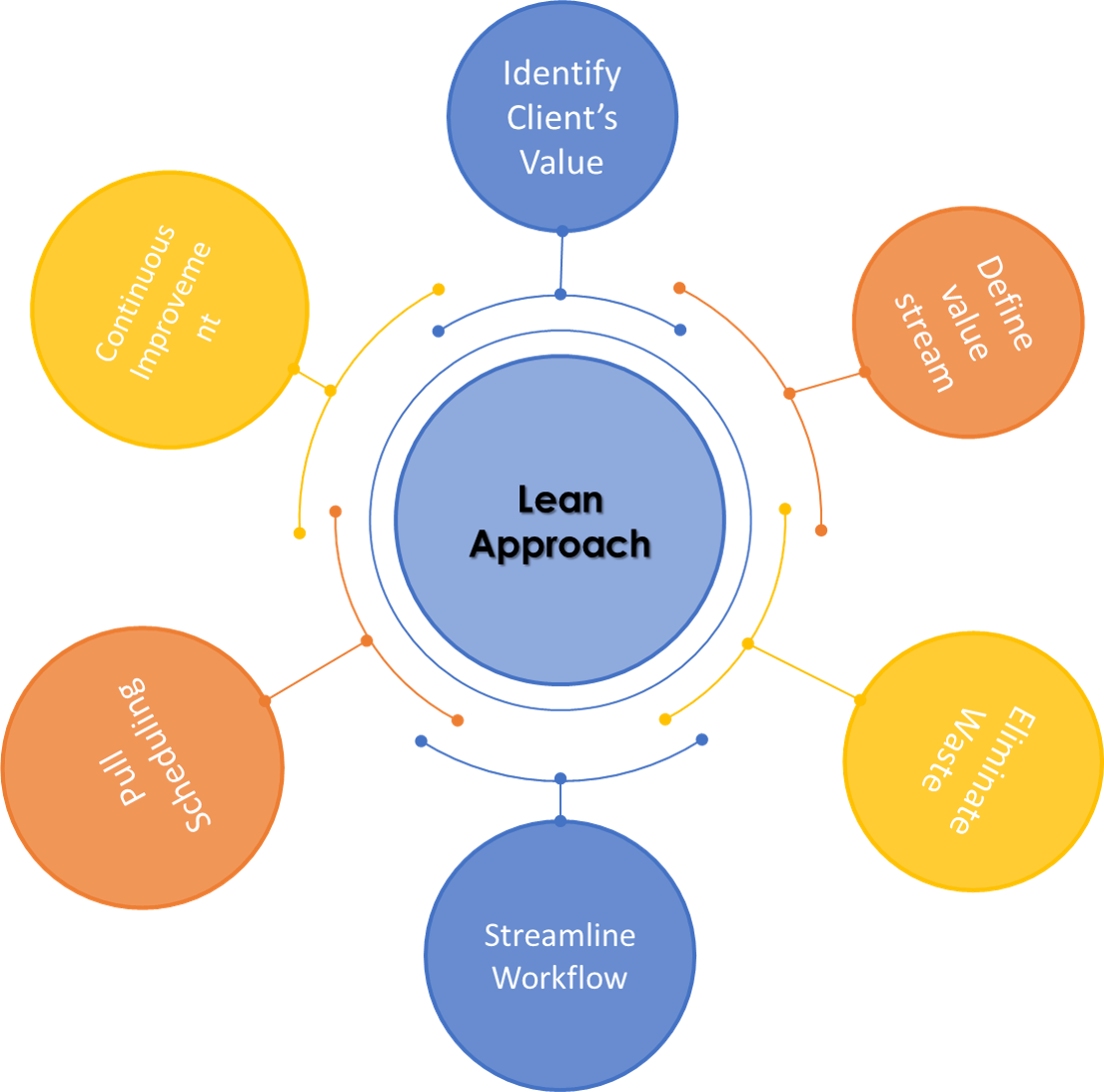
This method again has roots in Toyota Motors. This method was developed in the 1920s but was not implemented until after World War-2. This Approach was first coined by an international group of Lean Construction in 1993. It was initially adopted for the manufacturing process in a controlled environment, but it's led to the adoption of this process in a wide range of industries.
Lean Approach uses a wide variety of tools such as Last Planner System, Integrated Project Delivery, Kaizen Approach & Building Information Modelling. It has a wide range of tools present in the system which can be applied, which helps in providing a holistic approach to project management.
It has six principles as follows:
- Identify Client's Value
- Define Value Stream
- Eliminate Waste
- Streamline Workflow
- Implement Pull Scheduling
- Achieve Continuous Improvement
How is it used in Construction?
Lean Construction was adopted by contractors & management firms due to its high success rate. Lean Construction transforms every stage of Construction by demanding the involvement of workers from all levels, training needs, and expressing innovative ideas for a problem at hand.
It has helped in achieving on-time delivery of projects, increased customer & worker satisfaction, high quality, and better risk management procedures. Lean Construction is a popular idea for management firms to provide complete customer satisfaction & building a prestigious reputation.
4. PDCA Cycle:
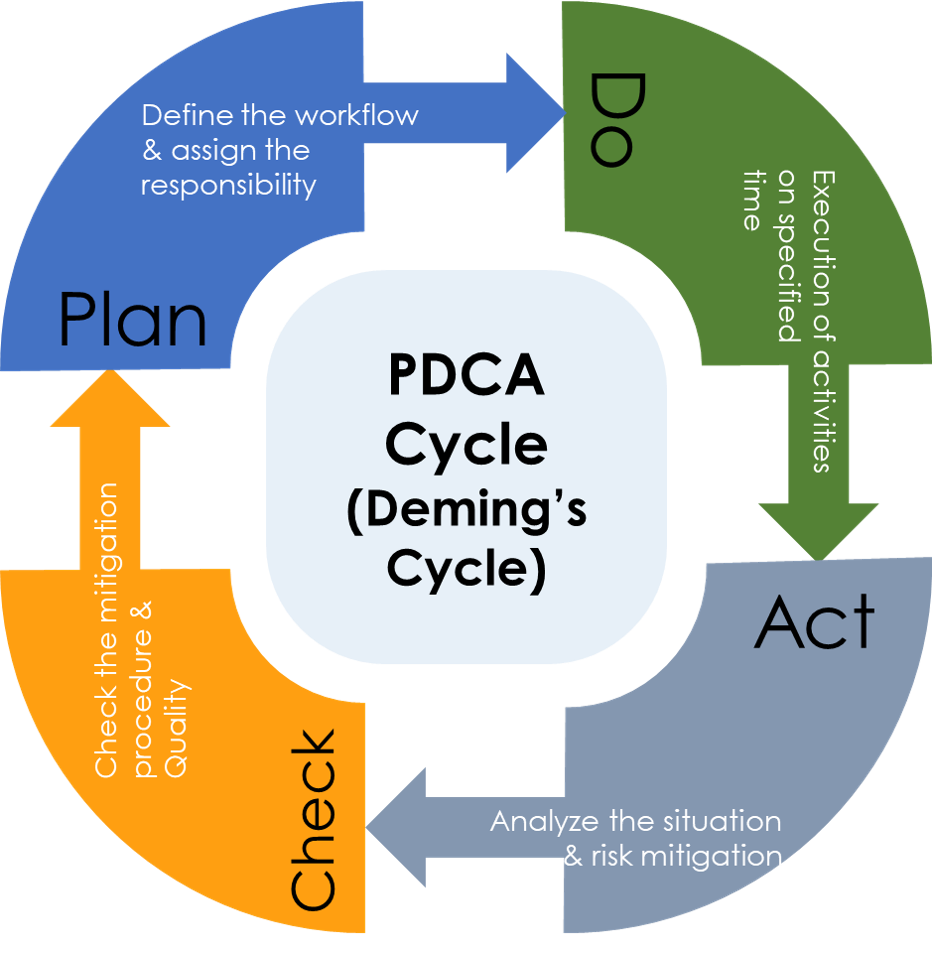
PDCA Cycle was first developed by a management consultant Dr. William Edward Demings, in the 1950s. It is also popularly known as Deming's cycle. This model helps in building a continuous loop for controlling & improving processes.
It helps in implementing a total quality management system through its four principles. This basic nature of the model helps continual improvement easily available and understandable for clientele.
Four principles of the PDCA Cycle are:
- Plan the activity: Identify opportunities or error
- Do: Implement a process for risk elimination or grabbing the opportunity
- Check: Analyze data & results of the process
- Act: Either accept the procedure or improve in order for better quality achievement.
How is it used in Construction?
PDCA Cycle has a wide variety of applications in the construction industry. It can be used as a total quality management system. It is easily applicable in the construction industry due to its basic nature.
PDCA Cycle generally helps the organization to build quality products, guarantees customer satisfaction, and helps in continual improvement through data-driven analysis. It also helps in guarantee that the mistake is not repeated in any further processes. Along with this, it also has a feedback system in place that helps in removing any communication gap between different levels of the workforce. This makes the workforce active in providing innovative solutions in their respective aspects.
Conclusion:
As we understand these approaches towards quality management, we also need to understand each of them personally modified with changes required for the construction industry. In the following stories, I will explain each of these approaches in detail with examples prevalent in the construction industry and how they reduce the amount of wastage & rework. These approaches also adopt a centralized quality control system in order for more effective quality control. The centralized quality control system, along with the PDCA cycle, is adopted by digiQC to provide the highest level of the quality control system.
Eager to know how digiQC ensures the best quality management? Check out the all new blog series from digiQC: Quality management in construction—An Overview to get an in-depth overview, right from the best quality experts in the industry.