Would you like to know why the industry prefers UltraTech cement over any other cement company? The other prevalent companies also have passed the same set industry standards. But have you ever wondered when we think of cement then ultratech is the first name that comes to mind.
The answer lies in the consistency of quality provided by the company. Over the years, it maintained the standard required for the construction industry. But let’s give it a thought: how would they have achieved such consistency?
The question can be answered with many key points. First, they would have hired trained and experienced scientists to formulate their product. They would have conducted research and would have facilitated highly equipped laboratories to do the same.
Hence, the cost of a bag not only includes the cost of raw material but also the cost of these aspects done in order to produce the best quality. But what are these cost? How can we provide quality products in budget rather than high cost-high quality products?
In this blog, we are going to help you understand cost breakdown structure of quality and how bearing a little more cost at initial stages may reduce overall cost of a project/product.
Cost of quality by definition is the cost incurred to ensure quality requirement and evaluate that the quality requirement is being met including any other cost as a result of poor quality being produced.
Cost of quality incorporates the cost of good quality & the cost of bad quality. The cost of good quality includes time, money & other resources used to provide the aforementioned quality. Cost of bad quality includes repair, rework, material wastage, etc. done to improve the poor quality delivered.
Cost of Quality = Cost of Conformance + Cost of Non - Conformance
According to the above mentioned equation the Cost of conformance & Cost of Non-Conformance contains a series of different construction activities.
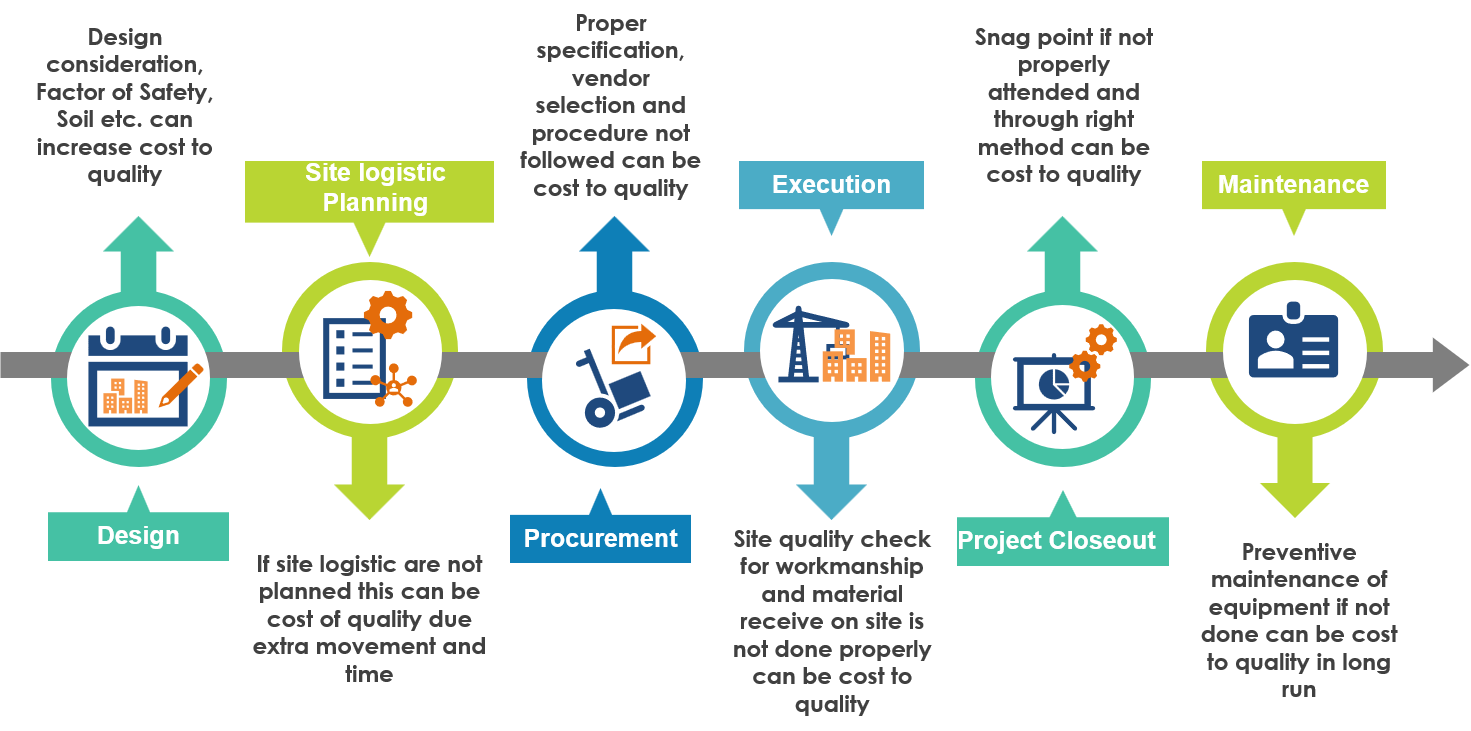
Cost of Conformance
It is a proactive stage of construction. It ensures that no defective products are produced in the first stage. Cost of conformance includes prevention cost & Appraisal cost.
1. Prevention Cost
Prevention cost is generally included in quality planning in the early stage at the commencement of the project. It provides the specification for materials to be used, testing of materials, site logistics, quality to be delivered & training to employees & laborers.
Site logistics is another important criterion for diminishing the cost of quality. As soon as the specification is provided, managers move towards the procurement of materials. This material is to be stored at the site for different construction activities. The material ought to be dumped such that they are at the proper place when required. If not, it needs to be moved to the desired location by site workers. This results in wastage of labor days & results in disruption of outlined schedule.
Testing of materials is vital for producing quality products. Cement, sand, aggregate, etc. are held to IS Standard to ensure the quality of construction. This laboratory testing is done batch-wise. This cost is included in the cost of prevention as it helps to avoid degraded quality through testing materials beforehand.
Training requirements, both for laborers & employees are critical. Skilled laborers are provided by labor contractors on hire. It is necessary to run a check on the qualification & work done by the contractor to support the claim. If not, an incompetent workforce can result in a loss of quality.
This is the area where the biggest gains are possible but is the most underrated part of the equation. Counteraction procedures such as training, quality planning, lessons learned analysis & Quality related information systems yield high results in a rate of prevention. This, in turn, guarantees customer satisfaction & project success.
2. Appraisal cost:
Appraisal cost is the contribution of different checks done for material, suppliers assessment, appropriate market value, quality audits & checking fixtures. Some of these checks are done in a proactive stage & some of them are done in a reactive stage.
Quality control measures the results coming out of a production process to determine what is going wrong and how badly. Appraisal often falls within this definition as well.
Factors such as Supplier’s assessment & checking the quality of incoming material along with appropriate market value evaluation are done in a proactive stage. These checks often show material degradation value. If it happens materials can be returned & replacement for a supplier can be demanded.
Quality audits are done by individuals that have expertise in assessment & provide significant guidance in case of errors. These individuals provide suggestions & remarks for improving quality. This proactive step ensures there is constant improvement by learning lessons through mistakes.
Combined Prevention & appraisal systems assure quality products are produced. They are called the cost of good quality & an integral part of the system. If these systems fail, they induce poor quality products resulting in internal & external costs. They are called the cost of poor quality.
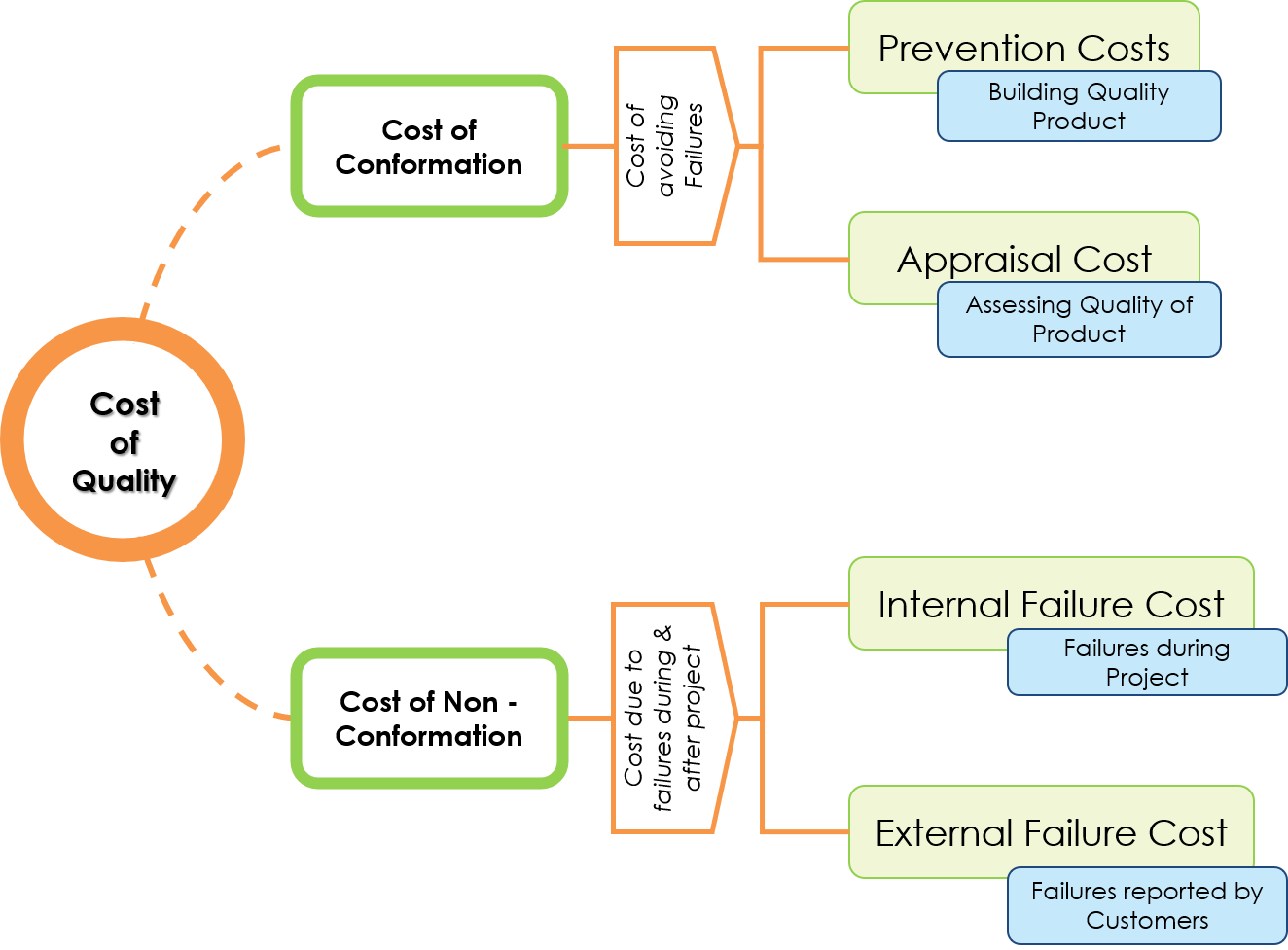
Cost of Non-Conformance
It is a reactive stage of construction. It is the cost endured due to defective products. It includes demolishing, reworks & maintenance. It includes internal failure cost & external failure cost.
1. Internal failure cost
The internal failure costs are the costs caused by deficiencies found before the delivery of products and services to external customers. These include either errors in quality production or errors in the manufacturing process.
For example, if M20 grade of concrete is to be produced for a certain structural element. The raw materials tested beforehand are approved by inspectors & still the quality is not achieved. This can happen if either the proper care is not taken during the preparation of the concrete or else the workmanship required is not up to the set standards.
It can be said for the aforementioned case that the design ratio provided to the site engineer is wrong, it is an error in quality production. The explanation is, that regardless of how exactly the technique for production was, the ratio was not sufficient to provide M20 grade of concrete.
In another case, the design ratio given was correct & would suffice the structural requirements but still, there was a failure in quality production. This means the process of manufacturing was correct but the way work has to be executed was not proper.
This example shows that internal costs can be due to the prevention & appraisal system. This results in rework & wastage of resources & raw material. This in turn increases the cost of production.
2. External Failure Cost
The external failure costs are the costs caused by deficiencies found after the delivery of products and services to external customers. This results in consumer dissatisfaction & holds high stakes in the company’s reputation.
These can be costs for complaints, repairing & redoing services, warranties, and environmental costs.
An example can be given if the builder has promised to provide a building with safe sanitation services & good quality ambiance in the building. During construction & audits no leakages or poor sanitation issues.
Now possession is given & within months, the plumbing system fails. This results in dampness & leakage problems in the house as well as in common areas. The faults may be the result of unknown factors or known factors taken lightly during the planning.
Since the consumers are facing such struggles despite providing the finances, they have the right to claim a warranty or rework in building services.
Such disputes, rework & maintenance work comprises external failure cost. The direct costs of failure are usually just a small part of the total cost to an organization, even if it’s the main focus of the project team. Loss of future business and reputation can be extremely costly but difficult to define.
3. Assessment of the cost of quality
For assessment of the cost of quality, PAF Model is developed. Prevention, Assessment & Failure Model aggregates cost on the level of organization. With the increase in spending on prevention (pro-quality) and assessment, the number of internal and external failures is reduced.
Internal costs are associated with poor quality as irreparable defects, and reclassification of products and external costs are associated with poor quality such as customer complaints and modifications, repairs, and exchanges of returned products.
This model has an organization level of breakdown which shortens the analysis & does not help in finding root cause problems for continual improvement.
The criticism of the PAF Model led to the development of the PCM Model. It is Project Cost Model & it divides costs into the cost of compliance & cost of non-compliance.
Cost of compliance is the lowest possible cost to attain quality (Staff, Equipment, Material & Environment) & cost of non-compliance are costs due to inefficient use of resources (errors & rework).
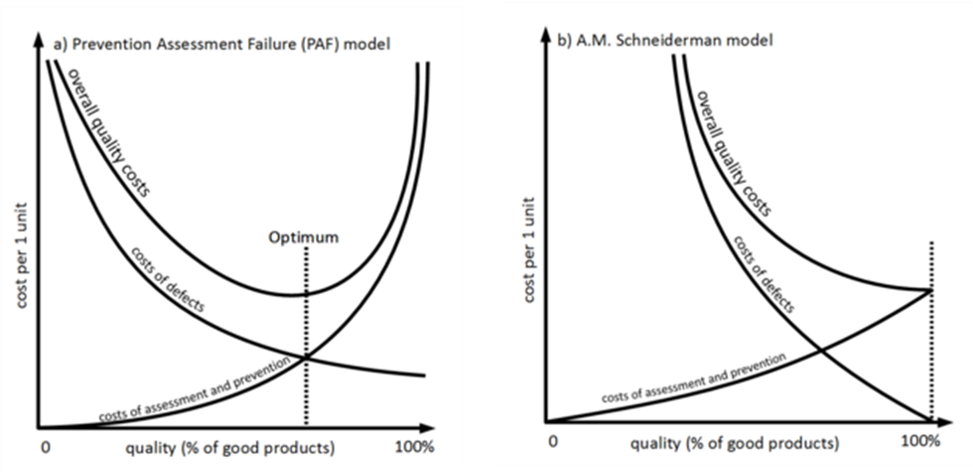
Conclusion:
As we have seen, generally cost of non-conformance i.e, failure in providing the predetermined quality results in budget overrun. It is best if we invest in quality management procedures in the proactive stage of project formulation. These results in providing us with insight into how proactive planning can help you reduce unnecessary costs and help in providing satisfactory quality.