In a developing country like India, the construction industry holds an important position, given its expected annual growth of 6.2% in the next 3 years With such steady growth ahead in the future, the industry is likely to value its projects more than ever, with a greater focus on time, cost and quality—the three ultimate variables involved in a project. In order to meet the high demand, the cost is carefully worked out by top construction professionals in India, to give rise to projects that are both high-performing and practical.
It is general understanding that the cost increases as the quality increases. But did you know that the cost also increases when the quality decreases?
Find out how by the contents of this blog that are gathered from the opinion of top experts in construction.
Not having the time to read? Reach out to us and hear all about the cost of poor quality and quality assurance from our expert team!
The Relationship between Cost and Quality
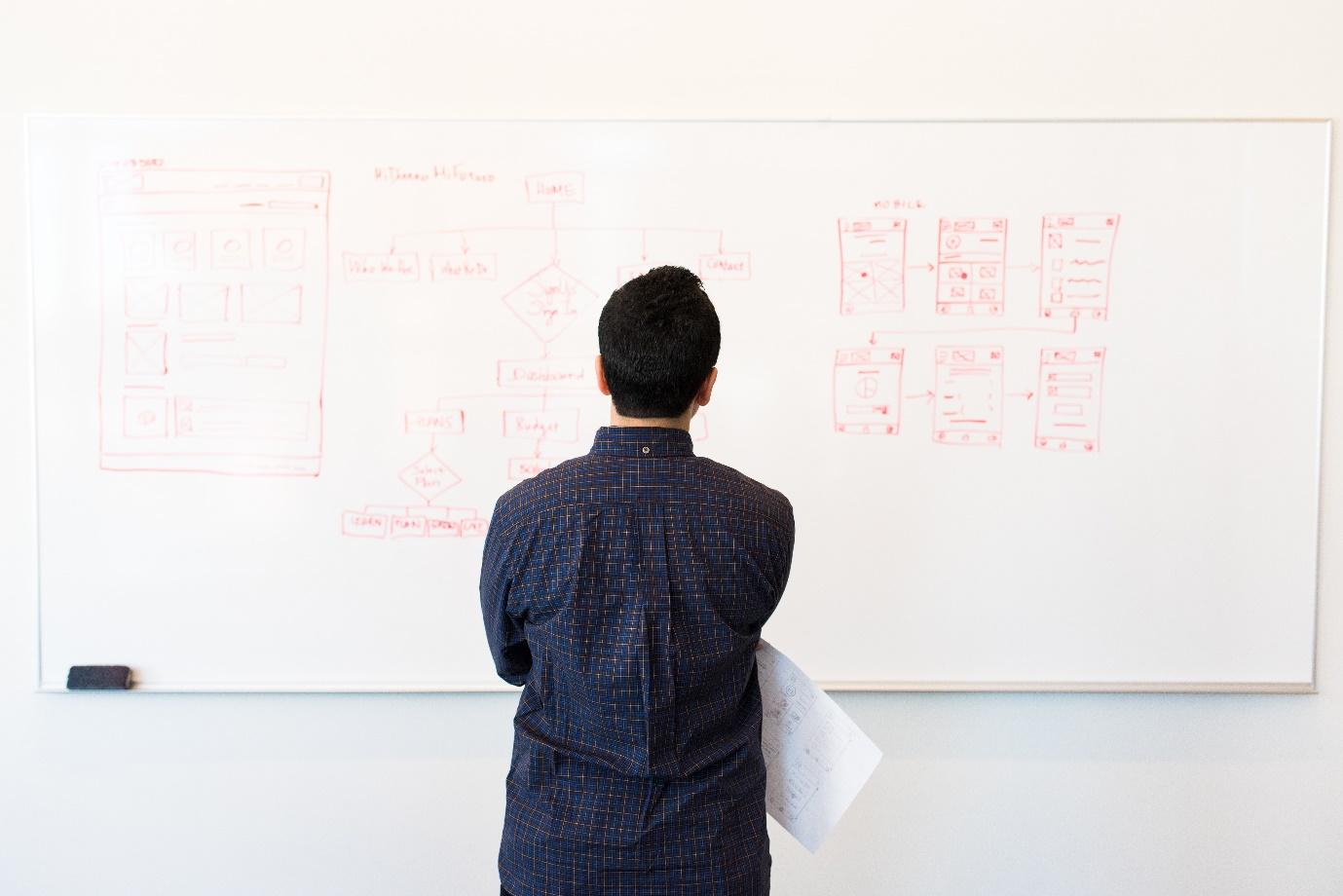
The cost invested in quality comes in a two-way system—first being additional the cost spent on high-quality materials and resources, with the second being the hidden costs compensated for the issues created by low-quality resources. While the former comes with a well-planned project plan that comes in line with the schedule, the latter comes creates an unexpected turn of events across the project’s plan including:
- The project schedule
- The resource allocation—both material and manpower
- The mitigation plans, among others.
These are labelled as Cost of Poor Quality (COPQ) and Quality Assurance (QA) respectively in the industry’s terms.
Quality Assurance: The definition
Quality Assurance is the deployment of systematic efforts to ensure that the materials and other resources are on par with the standard quality requirements. It is executed in multiple phases of work by dedicated quality assurance engineers who strive to achieve reliable quality benchmarks along with complete customer satisfaction.
A robust quality assurance involves the below costs:
- Prevention costs spent on trainings, certifications, management solutions etc.
- Appraisal costs spent on quality audits, verifications etc.
Read more about the costs in detail in our previous blog.
Amidst the sizeable investment in quality, it is favored by top experts in construction because of the fact that it is a well-planned measure that ensures the smooth flow of the project. In the absence of a proper quality assurance process, a project is affected by the Cost of Poor Quality (COPQ).
Cost of Poor Quality: The definition
Cost of Poor Quality (COPQ) is the cost incurred by the use of low-quality materials and services in a project. These are usually caused by the risks and failures occurring as a result of poor quality.
These Cost of Poor Quality (COPQ) typically includes:
- Internal failure costs incurred by rectification, failure analysis etc.
- External failure costs incurred by repairs, warranty claims etc.
It is typically calculated as
Poor Quality = Internal failure costs + External failure costs
These costs also cause a significant deviation in the project management process creating a number of issues that include:
- Delay in the schedule due to the repairs
- Financial losses due to material wastage
This indirect relationship adds accuracy to the calculation of Cost of Poor Quality (COPQ) with the below formula:
Cost of Poor Quality COPQ = (Waste + Defects) * Time spent on rectification
The Effects on Project Management
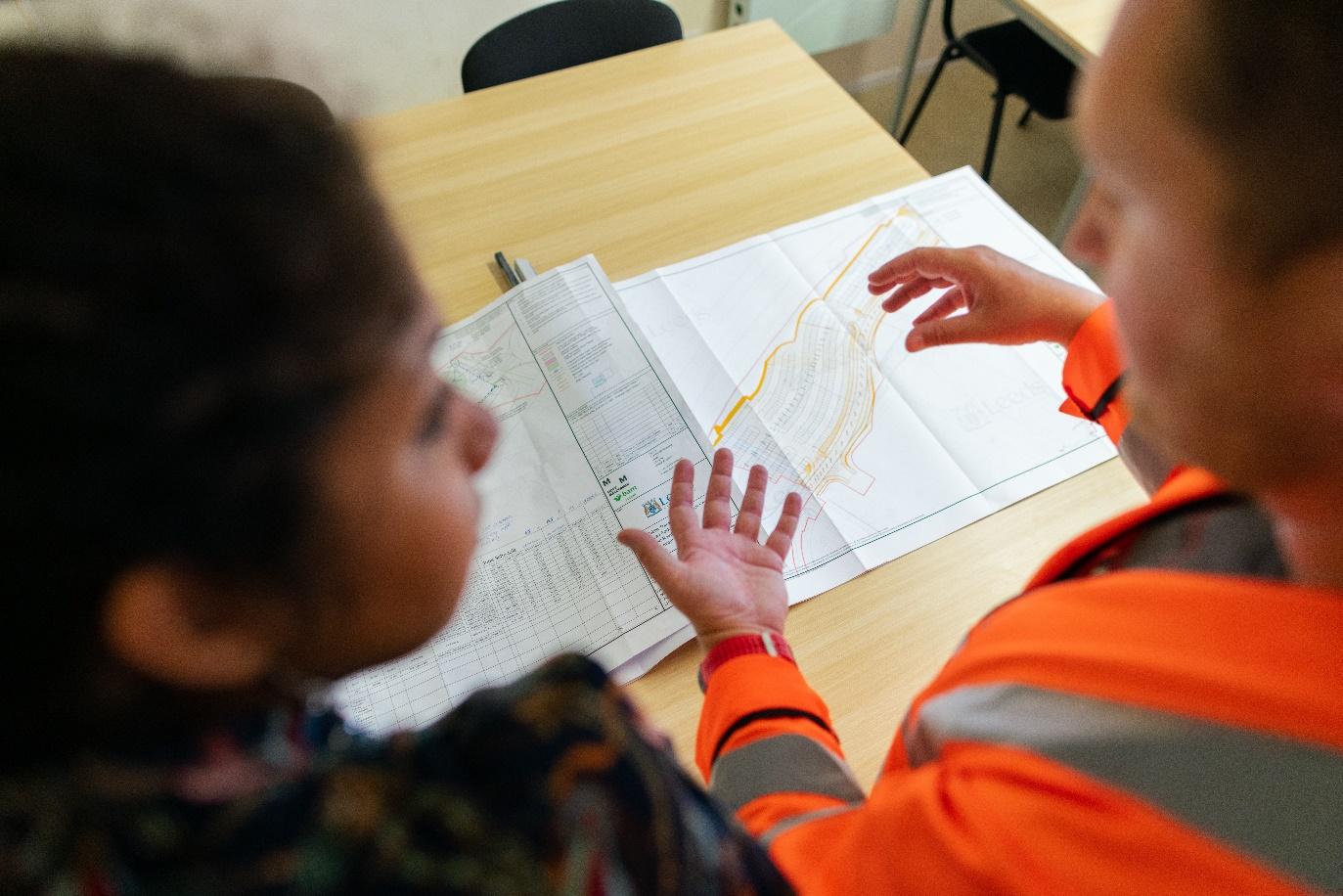
The cost spent on both quality assurance and poor quality have a profound effect on the project management process. While quality assurance makes it better with early identification and mitigation of non-conformances, the poor quality situation hinders the project management process with an unprecedented call for action. Yet, the calculation of the Cost of Poor Quality comes as the best immediate solution with a number of benefits including the below:
- It helps in prioritizing the actions for improvement
- It facilitates resource optimization
- It helps in identifying the wastage
- It restores the cycle of profitability
- It serves as a reference point for future issues
On the whole, it is essential to employ quality assurance whilst calculating the cost of poor quality to ensure seamless project management.
The Role in The Competition of The Industry
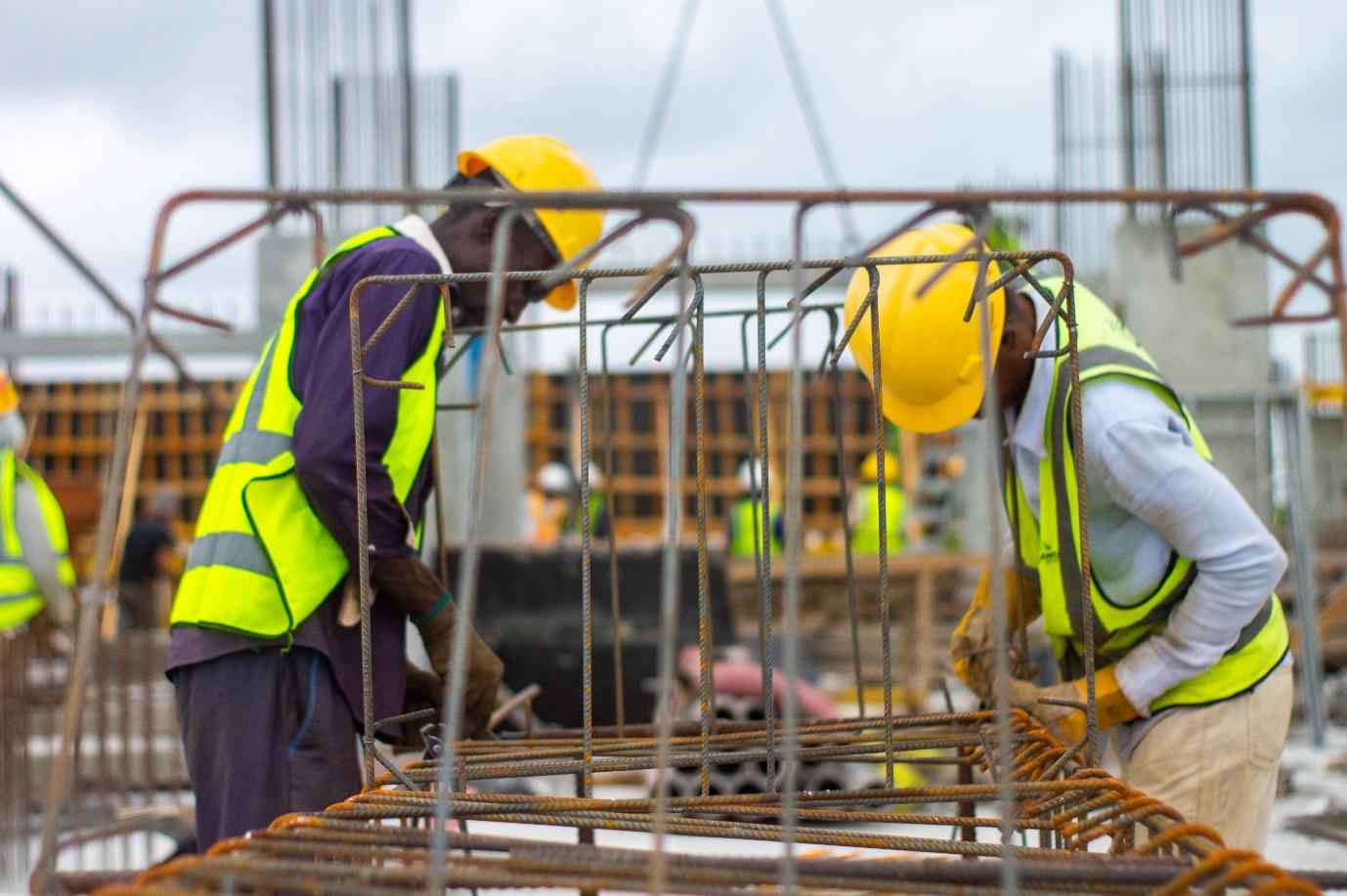
Quality plays a major role in upholding the reputation of a company. While an established quality assurance process secures a company’s position in the competitive industry, the Cost of Poor Quality (COPQ) ensures a healthy professional approach that makes a company stand tall both in the eyes of the client and the workforce. The introduction of such a system helps the company adapt to the rising demand of the industry amidst undergoing constant improvisation. This is essential to evolve and grow with the industry and its newer branches across management, innovation and digitization.
The Upgrade via Digital Solutions
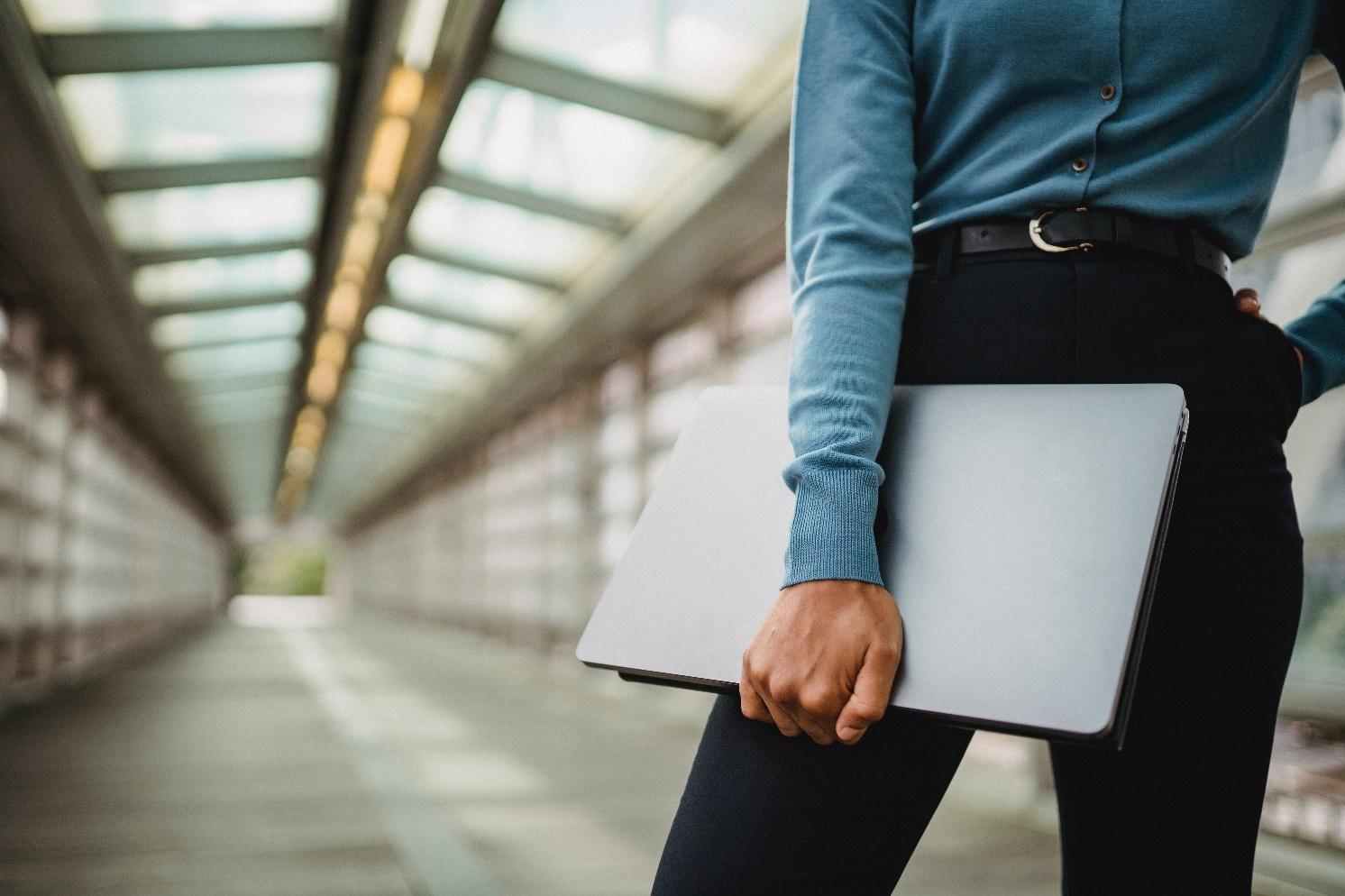
Digitization is the new direction of the construction industry. It simplifies all of the construction process from the planning till the quality assurance, to give a future-forward thrust to the construction practices. For quality, in particular, digital solutions come to take things beyond simplification, to new methods and practices that include:
- Online monitoring of quality-related activities from anywhere, at anytime
- Digital approvals dismissing the need for commute to on-site meetings
- Tracking the project analytics with software-computed insights
- Easy identification of quality issues and other related data, among others.
Such digitally-powered solutions, the quality variables are able to achieve greater accuracy in both change and effect, to give rise the projects that illustrate true value and performance.
Are you looking for a digital quality management solution that comes with all of these benefits?
Go to www.digiqc.com now!
About digiQC: The Best Quality Management Software you can find
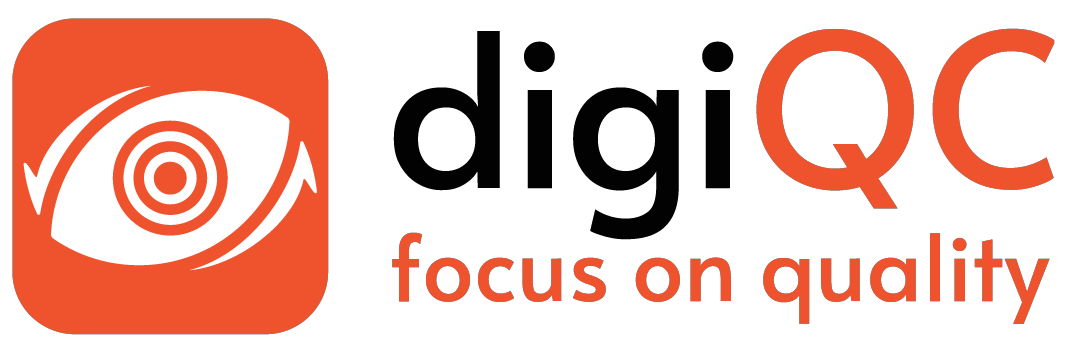
digiQC is a cloud-based software that inspects on-site work in real-time. It simplifies how you collect, store and retrieve your Construction Quality Checks. The key features include:
- Real-time quality checks
- Customized checklists
- Remote approvals from experts
- Secure cloud storage for key documents
- Instant notifications and more.
With the range of features, digiQC serves one purpose:
“To save billions annually by reducing rework and wastage”
Are you ready to save cost with a state-of-the-art digital quality software like digiQC?
Schedule a demo with us and see the benefits yourself.