In the construction industry, quality control is required to ensure the predetermined standards are being met during the execution phase. Although, standards set during the start of a project contain many specifications for a single item and need to be checked at a different stage of execution for stringent quality management. This is where the quality control checklist comes into the picture.
QC checklist is a very important part of quality control and affects various aspects of construction projects. For starters, the document helps in establishing accountability and transparency. At another point in time, it can help in root cause analysis for finding a solution to a problem. But all this is only possible if the proper checklist is prepared for which analysis is to be done. The checklist also helps to minimize the quality-related risks on the site if made properly. So, it becomes very important to prepare a checklist that does reduce the risk but can help in identifying the root cause in case of any issues on site.
Here are some necessary tips for creating a good quality control checklist for implementation in the quality control system.
Defining purpose:
Understanding ‘why’ we are creating a QC Checklist is very necessary. A few reasons to create an accurate QC checklist are mentioned below:
1. Quality documented trail of what and how work is inspected and what issue needs to be addressed.
2. Create awareness to minimize high-risk factors.
3. Establishing a central and hierarchal quality control system.
4. Record field inspection data for process improvement.
5. For doing root cause analysis for decision making and problem-solving.
6. Do it right the first time and avoid rework.
Guide to creating a quality control checklist:
The best way to improve your quality control checklist is to follow certain thumb rules established. Here is the list of guidelines to be followed when preparing a quality checklist:
1. Risk during the execution of work:
High-risk activities that can cause quality failure should also be considered while creating a checklist. This can be technical specification as well as common construction risks or issues faced across the construction industry. Also, safety-related risks are to be considered while creating a checklist.
For example, before doing flooring, it should be checked that all the service-related activities are completed, or else there be the risk of rework.
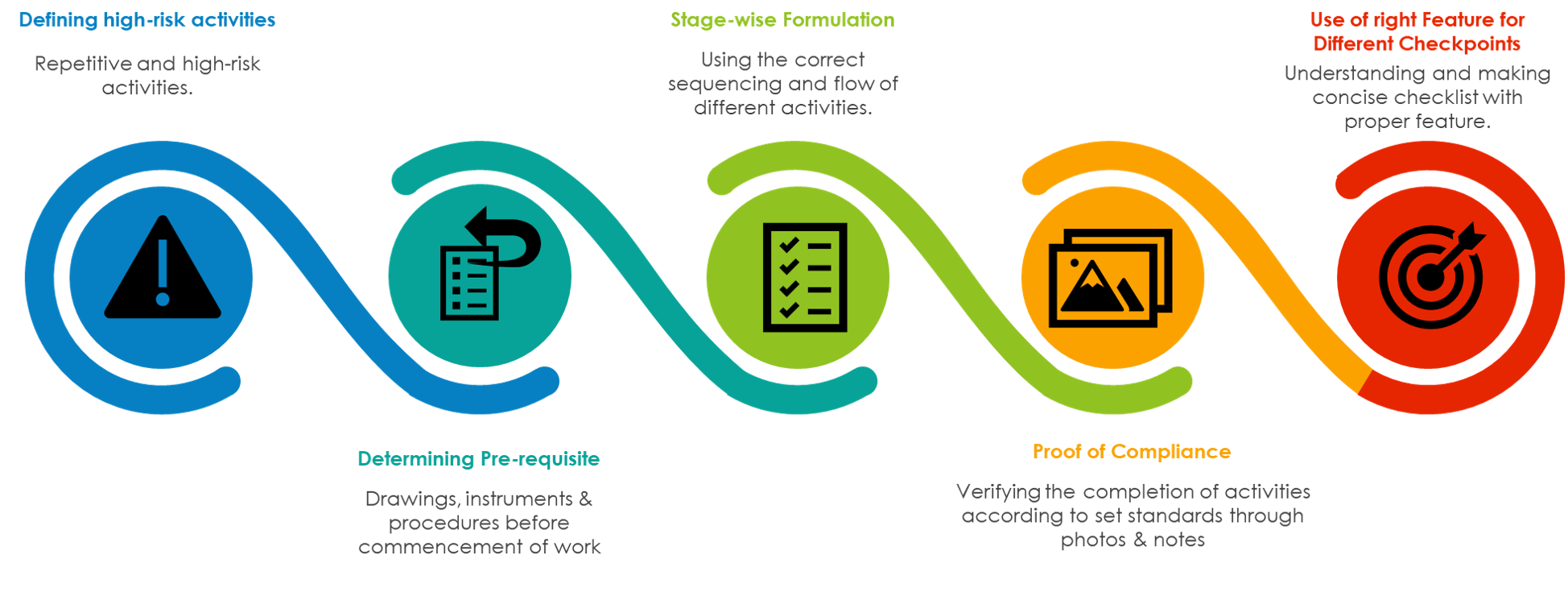
2. Determining Pre-requisite:
The next step for developing the checklist is a pre-requisite to completing work. This includes a list of items to carry to inspection, such as tape, plumb bob, level tub, etc. Another important pre-requisite is to carry the latest set of drawings. For other activities, pre-requisites can be different, but drawing remains mandatory for every activity. Taking an example of floor PCC, the pre-requisite is watering the earth for three days and using a mechanical compactor to ram the earth for another two days.
3. Stagewise formulation:
Stage-wise formulation of the checklist is very important. Every inspection for an activity should be ordered as per requirement.
Take an example of concreting of the column. First, column reinforcement should be checked as per drawings, and points such as lap length, links, and rings of the column in the proper place should be checked. Then formwork should be checked for the right angle, orientation, and level. Cover for concrete should be in compliance with drawings and IS Code. Now while concreting use of vibrator and surface tamping is required along with concrete quality is to be checked. After concreting is done, curing using jute bags is required, and if honeycombing is visible on the surface, it needs to be addressed.
Hence, pre-construction, execution, and post-construction checklists need to be developed for each activity with different checkpoints.
4. Accountability and transparency:
Checklists are created and filled during inspection to assure the quality of the item produced. Any discrepancy in checklists might lead to a conflict of interest.
Hence, the checklist should only be filled by an appointed person along with a witness present. This will bring transparency to the system. The same has to be recorded properly in case root cause analysis is to be done.
5. Proof of compliance for verifying stakeholders:
Proof of compliance can be given in the form of photos and notes during the inspection. This will provide a real-time experience of inspection to the one who is reviewing the inspection. Along with these, pictures with timestamps at the time of inspection shall be incorporated to ensure the photograph has been taken during inspection only. This is difficult in the case of paper format
6. Drafting checklist points question:
The drafting of checklist points should be such that the checklist points output from the quality control inspection can be used for root cause analysis. For example, some points may require “yes/no” as an answer, some points might require information to be captured, such as the name and revision of the drawing referred, and some points might require numeric value input. So it becomes absolutely important while preparing checklist points.
The language used should be simple and specific so that field personnel can easily understand and have proper options of answers.
For example, for concreting checkpoint for a grade of concrete should have options of selecting the selection the grade from the multiple-choice answer as this will be easy for the inspector to answer.
Questions that should be included in every Quality control checklist
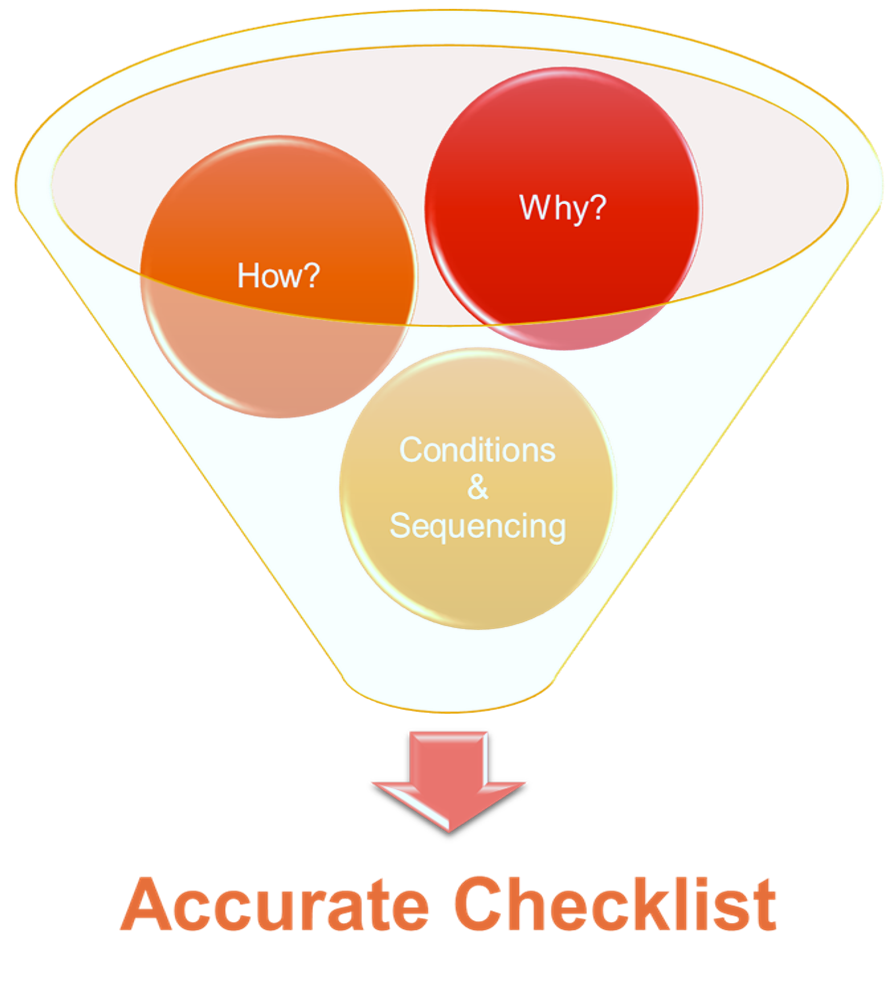
1. Project details.
2. Location of quality control.
3. Drawings or specifications are referred to while doing quality control.
4. Details of all the witnesses while doing an inspection.
5. Date and time of inspection.
6. The agency that executed the work.
Pros if the quality checklist is properly created
If the checklist is prepared with the above guidelines, then it will not enhance the way quality control is done but can help in the future for process improvement:
1. Reduction in rework and early detection of point of failure.
2. Reduction in maintenance costs due to proper quality checks.
3. The project timeline can be achieved as rework is eliminated.
4. Increase in goodwill and future bids of projects.
5. Benchmarking practices of quality control to increase client satisfaction.
6. Quality data is available for data analysis.
7. The root cause of data will help in decision-making and process improvement.
The essence of the blog
Quality is the uttermost priority in the construction industry. Construction material, goods, and services being costly, proper quality control may help in reducing rework and maintenance costs. This will help to deliver a project on time and within budget.
This can be achieved if a quality control checklist is properly created and implemented as a part of quality management. This will not only help improve the quality of the current project but also help process improvement and decision-making for a future project through the data available through quality checklists.
With digiQC, you can create a standardized and customized quality control checklist to fit the requirement of the project. To understand this, use the templates provided by digiQC. These templates are of great help as they cover key points to be considered while constructing a specific project.
You can also refer to the case studies and get an insight into how digiQC helped stakeholders to increase efficiency and provide early delivery of a project. These are backed by facts, statistics, and data taken from real sites where digiQC was implemented.
Now that you know your solution, are you curious about your quality management protocols? Read our exclusive blog series: Quality management in construction—An Overview and learn more about the different techniques and approaches for your next project.