Today we're going to take Kaizen Approach up close. But first, let us find out where this methodology developed. The definition of kaizen comes from two Japanese words: 'kai' meaning 'change' and 'Zen' meaning 'good' which combined gives the term "continuous improvement" This concept was first introduced in the 1980s by the Japanese car company Toyota.
Kaizen method believes in achieving quality improvement by developing habits of making small but significant changes.
The construction industry has three major aspects: Capital, Time, and Quality, and Kaizen Approach focus on these three aspects. Earlier construction organizations planned two elements for customer satisfaction. For example, if the client demanded the completion of a project on time with high quality, the expense was greater. This ideology changed as people expected good quality & timely delivery of projects on a budget. This led to the development of different methods of achieving customer satisfaction. Prime principles of the Kaizen Approach are explained here with leading examples.
Principles of the Kaizen Approach are:
1. Discover improvement Potential:
It includes defining the problem and making an observation on a daily basis on each and every aspect of activities. Then kaizen requires to point to significant improvement opportunities by analyzing and comparing the quality required and holding them to higher standards.
Improvement potential can be categorized into methodology and technology. For example, if the concrete is done using an on-site mixer and is transported through manual labor, it takes longer than ready-mix concrete transported through a pump. But the capital required might be a little high. This need to be decided in the next step on the basis of client requirement.
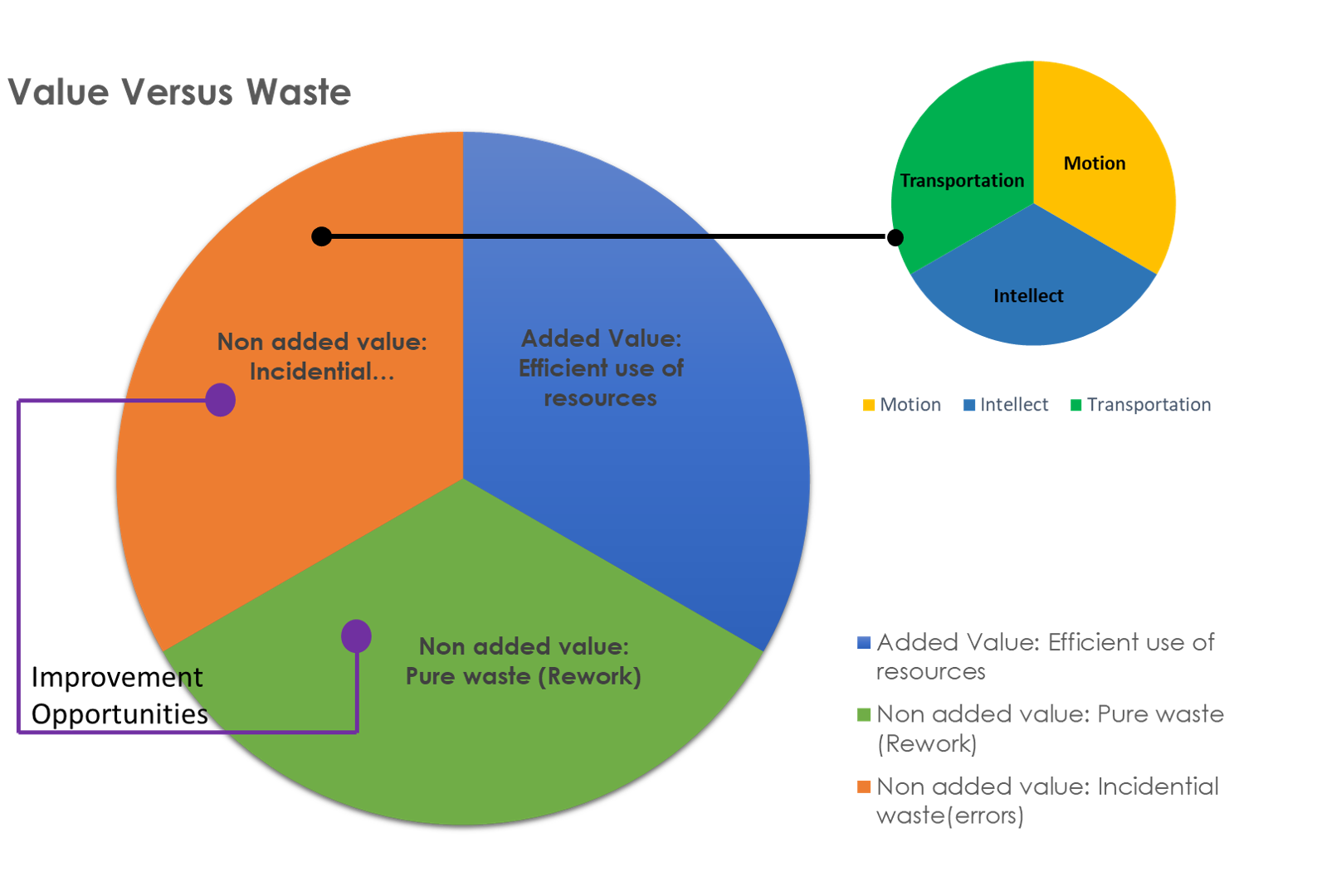
2. Analyze current methods:
Analyzing current methods in comparison to going trends in the construction industry and determining if the current method is updated to the site context. It requires the observer to organize and categorize the current method's drawbacks and their impact. This needs to be quantified and requires specific detail regarding material, method, and equipment. This helps find the root cause and shows various chain activities that require definite improvement. This is the most critical step in this process, and everything depends on decisions made on this level.
Now, the method of concrete needs to be analyzed, and what is the main focus for the client. Does he demand the project completed in the desired timeline with the capital, or is he ready to invest a little extra in order to complete construction faster? If either option is selected, improvement and planning are still required to provide guaranteed quality.
3. Generate Original Ideas:
For developing new ideas and strategies, various methods are used by the kaizen method. It includes brainstorming sessions, 5 W's 1 H, What if, Listing characteristics, Listing Faults, NHK Method, and many more. This helps in creating new ideas with healthy competition among employees and brings out a creative solutions for problems. This is done with every level of the workforce to get creative solutions across the team by deploying the most important resource- humans. This is very beneficial as creative yet simple solutions can even be learned from even a common worker in the organization.
4. Develop Implementation Plan:
For this step, workflow diagrams and time cycle analysis are required. Key points to be considered are the required time for procurement, execution, and buffer required in case of a new problem. Quality is defined, and it is the outlined quality to be achieved. There is no compromise in this factor, and it requires deploying all the necessary resources to uphold the standard.
Also, the work breakdown structure requires appointing responsibilities. This responsibility needs to be assigned based on the potential and skills of an individual. The implementation also requires each and every team member to communicate properly and express concern without hesitation to authorities above them.
The risk mitigation processes also need to be discussed, and the workforce needs to be trained to handle stressful situations with an integrated mindset.
Now, the client decided to go with ready mix concrete. Then quantity needs to be decided along with the time at which it is required. It also requires a market feasibility study and selecting the best available option. Also, sometimes the pump is clogged due to some technical error. Then the site engineer needs to take quick, decisive action because concrete becomes stiff as time passes by. The risk mitigation step planned help, such as the availability of a technician or member knowing the mechanics of the pump.
5. Implement the plan:
It is the responsibility of major stakeholders to create a positive and safe environment for the plan's successful implementation. Communication and upholding responsibilities are the key factors in the implementation plan. The plan needs to be carried out as per the regulations provided, and quality checks should be carried out regularly to check the process.
6. Evaluate the new method:
Evaluation of a new method decides whether the new method is beneficial or not. It verifies every aspect of the procedure and analyses the data. Pros and cons list made to identify the faults and new improvement potential.
The main focus of the KAIZEN Method – Elimination of Waste
The above principles are deployed with one major focus on eliminating waste. Waste includes rework and material wastage and factors such as delay in supplies, wrong allocation of intellect, etc. There are six types of waste identified in the kaizen method, which the construction industry can be associated:
1. Waiting for supplies: Delay in the procurement of materials and required equipment & tools to carry out the activity.
2. Motion: Extra physical and mental strain that doesn't add value to the process
3. Transportation: Moving the materials and equipment to the desired location inside the construction site.
4. Inventory: Storage of material and equipment for the next activity and
5. Defect: Reprocessing or rework due to technicalities and human errors.
6. Intellect: Wastage of valuable human resources on non-essential modifications and not appointing skilled individuals to the desired location.
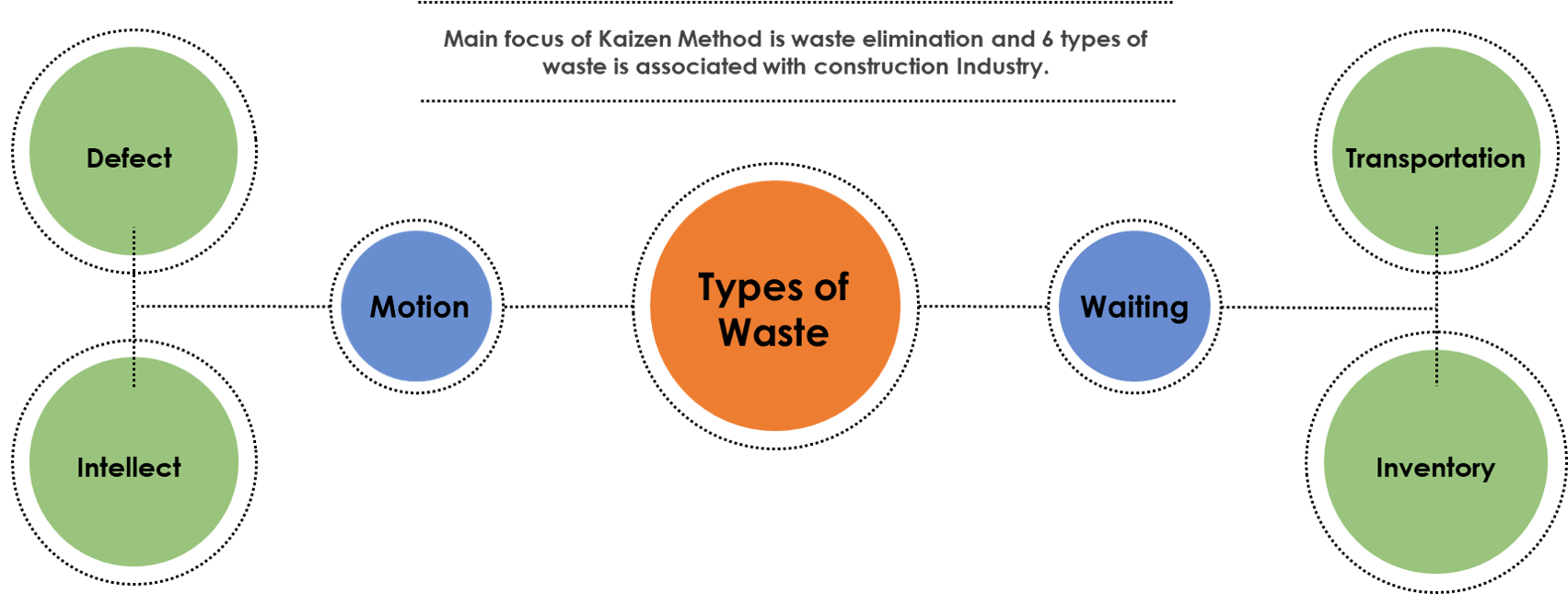
Advantages of the Kaizen Method
Listed below are the advantages of implementing the kaizen method in an organization:
1. Continuous Improvement methodology.
2. Engagement of different levels of the workforce
3. Increased Efficiency of Activities
4. Increased workforce productivity
5. Waste Reduction
6. Increased profit margin
7. Improved quality within budget
Drawbacks of Kaizen Method:
Drawbacks of the Kaizen Method are:
1. Training needs: People in the existing organization require new training to implement a new management approach
2. Resistance from employees: Employees deny shifting or changing values as change is unsettling.
3. Expensive & Uncertain: Implementation of this method is hard and expensive as tools used by the method require new technologies, and success depends greatly on the involvement and adaption of the workforce to the new changes.
4. Bad Change: As results take time to reflect, people might assume that the method is not successful and is a bad change compared to the traditional method.
Conclusion:
The Kaizen method is a high quality management approach applied widely in the construction industry. This can only be achieved if the entire workforce has a positive attitude towards the approach and maintain enthusiasm throughout the life cycle. New organizations might find adopting the kaizen approach easier than existing organizations with old management systems. This might take time to reach every department of the organization and reflect beneficial results. Kaizen uses a cost reduction procedure that helps achieve quality within a budget. The following chart shows the concept of cost reduction used by kaizen:( Reference- Ronald L. Turket)
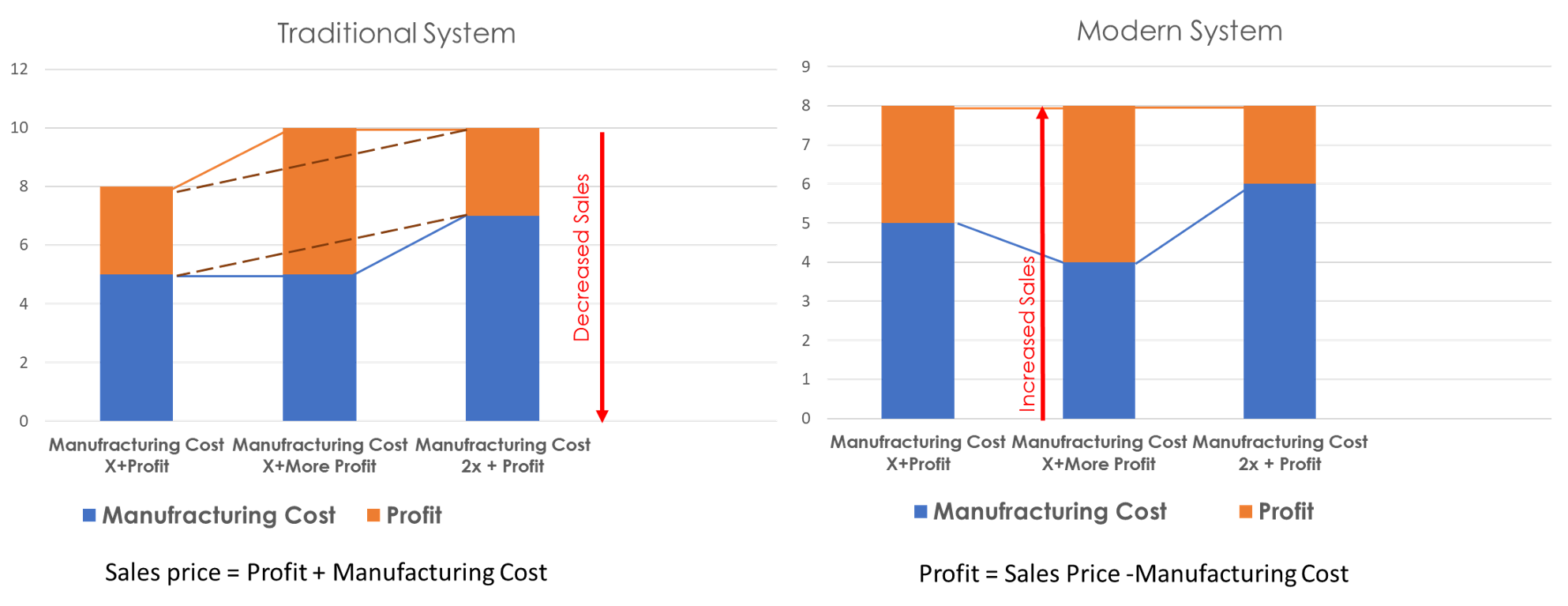
Thus we can try our best to adopt these high-quality approaches and take quality control to the next level for the construction industry.
Eager to learn more about the different approaches to quality management? Read our comprehensive blog series: Quality management in construction—An Overview