As we discussed earlier, the lean approach is widely adopted in the construction industry. The reason behind this is simple, basic steps with high yielding results. But what is the lean system? What are the principles of the lean approach? How does it benefit the construction industry?
All your questions will be answered in this story but first, let us understand how the lean approach was developed!
Lean methodology is one of the techniques which focuses on customer satisfaction through quality. It was first introduced by Toyota Motors in the 1920s but was not widely applied till World War-2. The international group of Lean Construction first coined this approach in 1993. It was initially adopted for the manufacturing process in a controlled environment, but later, it was successfully adopted in a wide range of industries through some lean modification approaches.
The lean approach is a holistic quality management approach that uses a wide variety of tools. Lean construction divides the whole process into two main aspects: Planning and Control. It uses its six principles to achieve continuous improvement, providing efficiency and reducing wastage.
Now, we will be discussing the principles of lean-approach.
Principles of Lean Approach
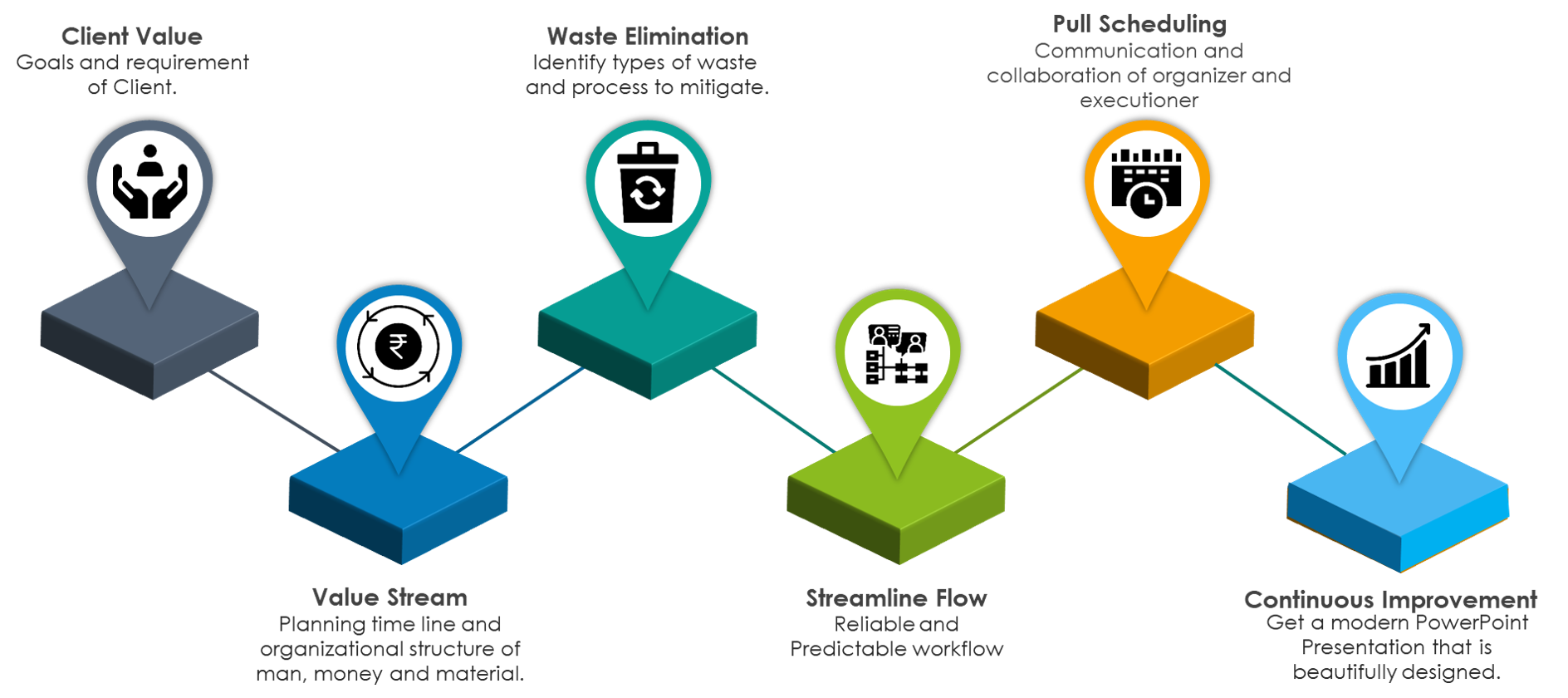
1. Identify Client's Value: Defining the Client's value requires defining what the client wants to build along with What they set the goals and what are the client's requirements so that the required quality can be achieved. Every stakeholder of the project, i.e., Architect, Project Manager, General Manager, Engineer, etc., has an open discussion to understand the client's requirements. They also provide advice and consulting to the client to shape his expectations as the project succeeds.
2. Define Value Stream: Value stream is laying out all the processes and planning the timeline as per the client's requirement. It defines man, material, and machinery required, where, when, and in which condition. Defining the value stream is the most important stage of this approach as it defines the timeline and budget of the project.
3. Eliminate Waste: Lean approach identifies eight different types of waste. The lean approach focuses on minimizing waste and reworking through different types of tools.
4. Streamline Workflow: Reliable and predictable workflow stream is a key feature of the lean-approach. This helps in the commencement of activity and reduces the stress of errors occurring when activity is performed.
5. Implement Pull Scheduling: This step recognizes the task that needs to be done, but planning and scheduling are done with the person's recommendations. This helps in communication and collaboration among employees and the management team.
6. Achieve Continuous Improvement: Continuous improvement is the heart of lean methodology. The main focus here is to eliminate waste, optimize current processes, develop new techniques for the betterment of future processes and continuously monitor and analyze data to rectify defect when it occurs.
Types of waste in the Lean Approach
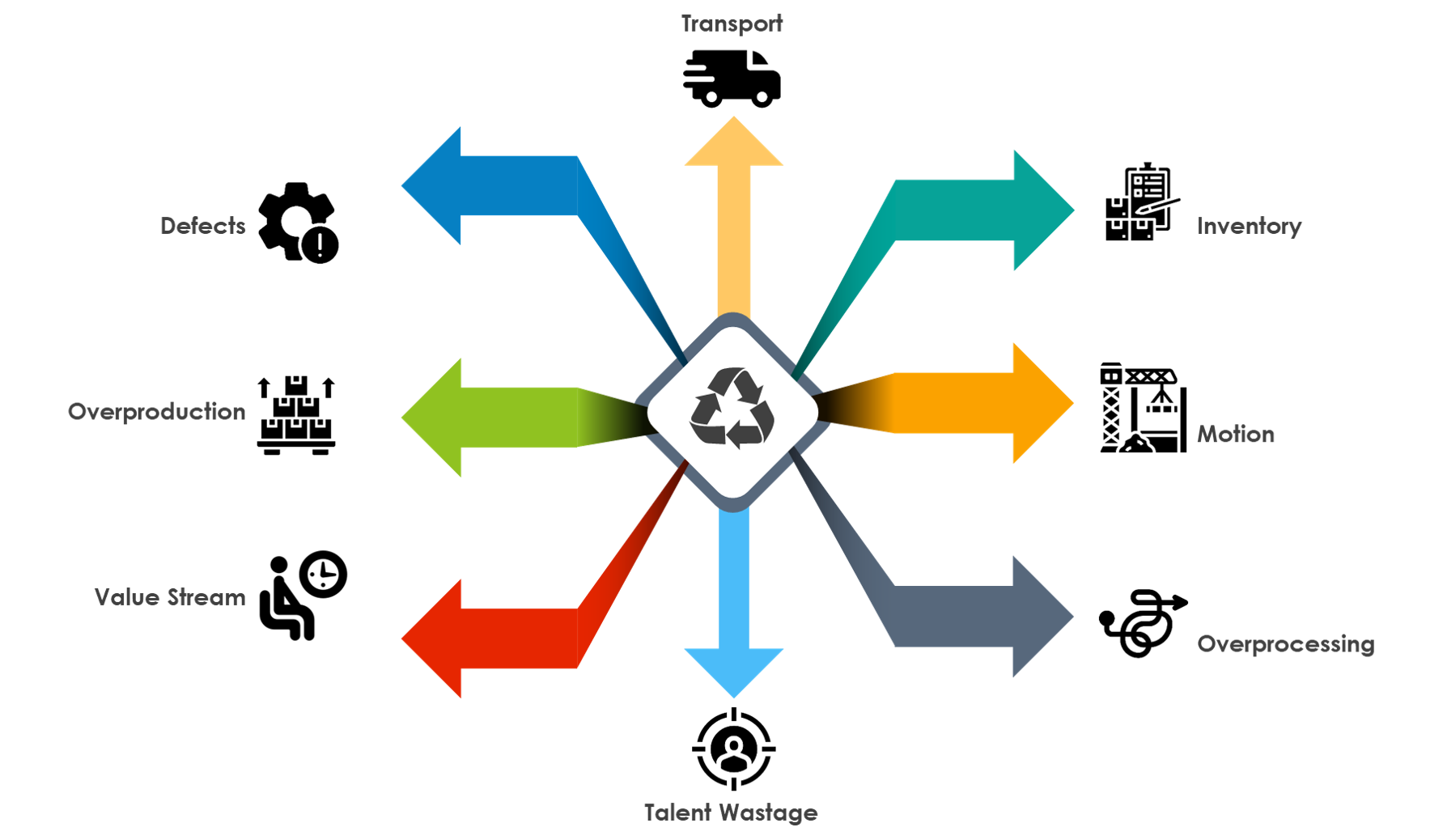
Eight types of waste identified for the lean methodology are:
1. Defects: The errors that occur and the rework and reprocessing are classified as defects. In simple words, not doing things correctly the first time is a defect. Elimination of defects is done through extensive planning and strategic vision. In order to eliminate defects in a construction site, the quality process should be standardized to have better control and communication.
2. Overproduction: Over-production is defined as the completion of a task beforehand. This provides the workforce with idle time, and the new processes cannot begin because procurement is not yet completed. The construction process shall be planned such that no stoppage of work is there on site.
3. Waiting: This is the most common phenomenon occurring in the construction sector. Workers are ready, but equipment, material, or pre-construction procedure is not completed, which leads to waiting and delay in work. The procurement along with site construction shall be properly synced such that required material is available on-site at the right time and right quality. This will not block the cash flow, and material can be properly handled on-site.
4. Not utilizing talent: When the right person is not appointed to a task requiring skills and experience, the talent is wasted. Thus, the allocation of talented and resourceful human resources is required and is an important task. Finalizing the vendors/contractor plays an important role in construction. If not done with pre-qualified criteria, there are chances of rework, which increases project cost and time.
5. Transport: It's an unnecessary transformation of information. Typically, it can illustrate with the example of material reaching the site before it is required. Also, site logistic is important to do smooth activities on site
6. Inventory: Material not required for current ongoing activity is excess inventory. This is a storage of extra material on-site and labor required for the movement of materials.
7. Motion: It is unnecessary motion due to distance between materials and labor and unnecessary transportation.
8. Over-processing: The addition of extra activities to eliminate waste is called over-processing. Unnecessary steps and precautions lead to over processing and wastage of resources.
Advantages of the Lean Approach:
The advantages of the Lean approach are as follows:
1. Reduced Wastage: Wastage is reduced by the elimination of rework and errors in construction activities. This helps in the reduction of overall cost and helps in achieving customer satisfaction.
2. Reduction in Construction Timing: The strategic planning and focused vision with predetermined goals help reduce error and increase efficiency. This also adds to the advantage of cost reduction because as time increases, there is the possibility of budget overrun.
3. Increased Site safety & worker's Satisfaction: The predetermined task and responsibilities help the workforce to understand and focus on the task at hand and evaluate the possible risks associated with it.
4. Communication Gap: The approach requires coordination and cross-function among departments. This increases transparency and accountability among the workforce.
5. Increased Profit Margins: This approach helps in achieving the promised quality during the quality assurance stage. Thus, it helps establish performance commitment and build a reputation as a prestigious organization.
6. Improved Scheduling: Strategies for risk mitigation and proper planning makes a schedule more reliable and predictable. This helps in reducing workload and stress. This provides a healthy work environment.
Drawbacks of Lean Approach:
The drawbacks of the lean approach are as follows:
1. Break-in Chain: All management and the workforce areas have to work along effectively. Predication from even one department can lead to collapsing of the whole system.
2. Training & management: Training employees for a new system is difficult. Management of human resources is a responsibility that should be taken very seriously.
3. A temporary decrease in Employee Morale: Since adopting new changes can be challenging; it leads to a decrease in inefficiency. This reduces morale and leads to stress development.
4. Ambivalent attitude towards change: Change can be scary and pose new challenges to every task. Thus, the workforce might have mixed feelings about new technology, and sometimes negative opinions become more popular.
Conclusion:
Hence, one can say no system is without defects, but with a proper management system and giving it the correct amount of time, the issues can be resolved. The lean approach is widely adopted as a quality management system due to its benefits and because this model gives highly efficient results. Although developed for a controlled environment, the lean methodology can be adopted for wide-scale use such as construction and provide high customer satisfaction.
As we are about to conclude these approaches with one last remaining PDCA cycle, we will move forward to how to make a quality control checklist. This, combined with a centralized quality control system, a digital tool such as digiQC, and the adoption of high-quality control approach, will recognize the organization as high quality producing firm. This, in return, will benefit society and help in providing high-quality service to clients within budget.
Find out more on the approaches to quality management in the all-inclusive blog series from digiQC: Quality management in construction—An Overview