The construction industry is unlike the other industries—it functions as a tool for building the future of our cities. With the rising expectation from the industry over the years, there has been a greater focus on its setbacks—especially when compared to the other industries like the manufacturing sectors that have shown faster growth during the time. The comparative analyses highlight a number of factors influencing an industry’s growth—among which quality factor stands out, making it an urgent call for the construction industry to revisit the current standards.
If you need a quick fix to your quality-oriented issues with the best quality management practices, head straight to www.digiqc.com and reap the benefits of the future-forward digital tool.
If you’ve got 10 minutes, read ahead to understand how the construction industry is lagging in quality standards and how this understanding can benefit the professionals on the whole.
Why compare construction and manufacturing sectors?
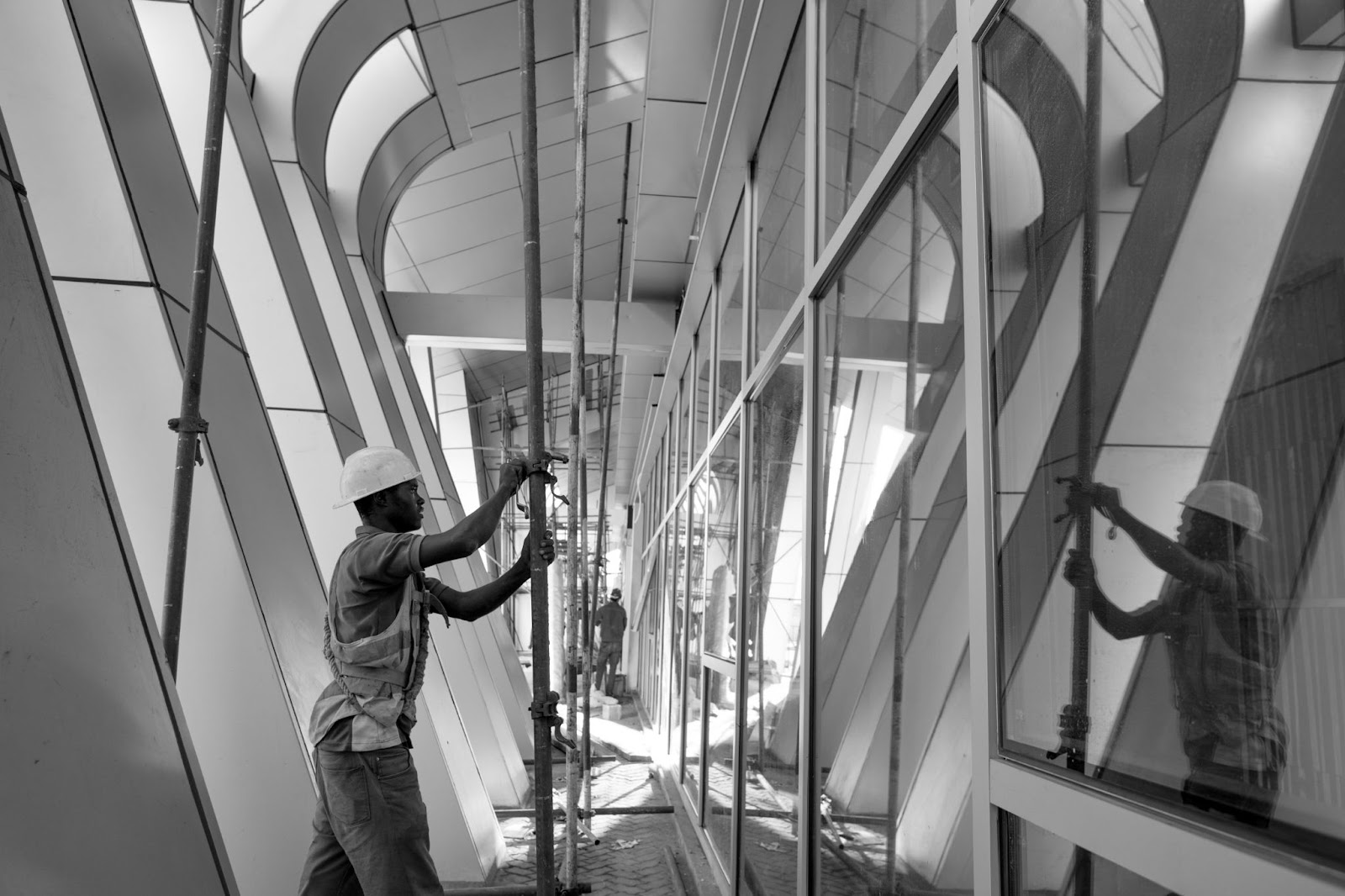
The construction sector has been subject to great growth and greater priority in modern times. This rise in expectations calls for a stronger comparison—with an industry that has shown greater progress than it. Manufacturing sector poses a strong debate in this comparison, for it has achieved a far organized pattern of work both on-site and off-site. Despite having the best talents, construction sector is yet to match their clarity in the workflow. The construction experts with great qualifications and multi-level thinking abilities are seen to lack the analytical mindset—while the manufacturing professionals have been acing it with nothing but practice. This makes it evident that by adopting similar practice-based knowledge systems, construction sector can also achieve a similar growth in the given area.
Such constructive criticisms and comparisons can give a direction for the industry to rise and progress. Take a look at other parameters of comparison and discover the solutions:
The challenges in the nature of work
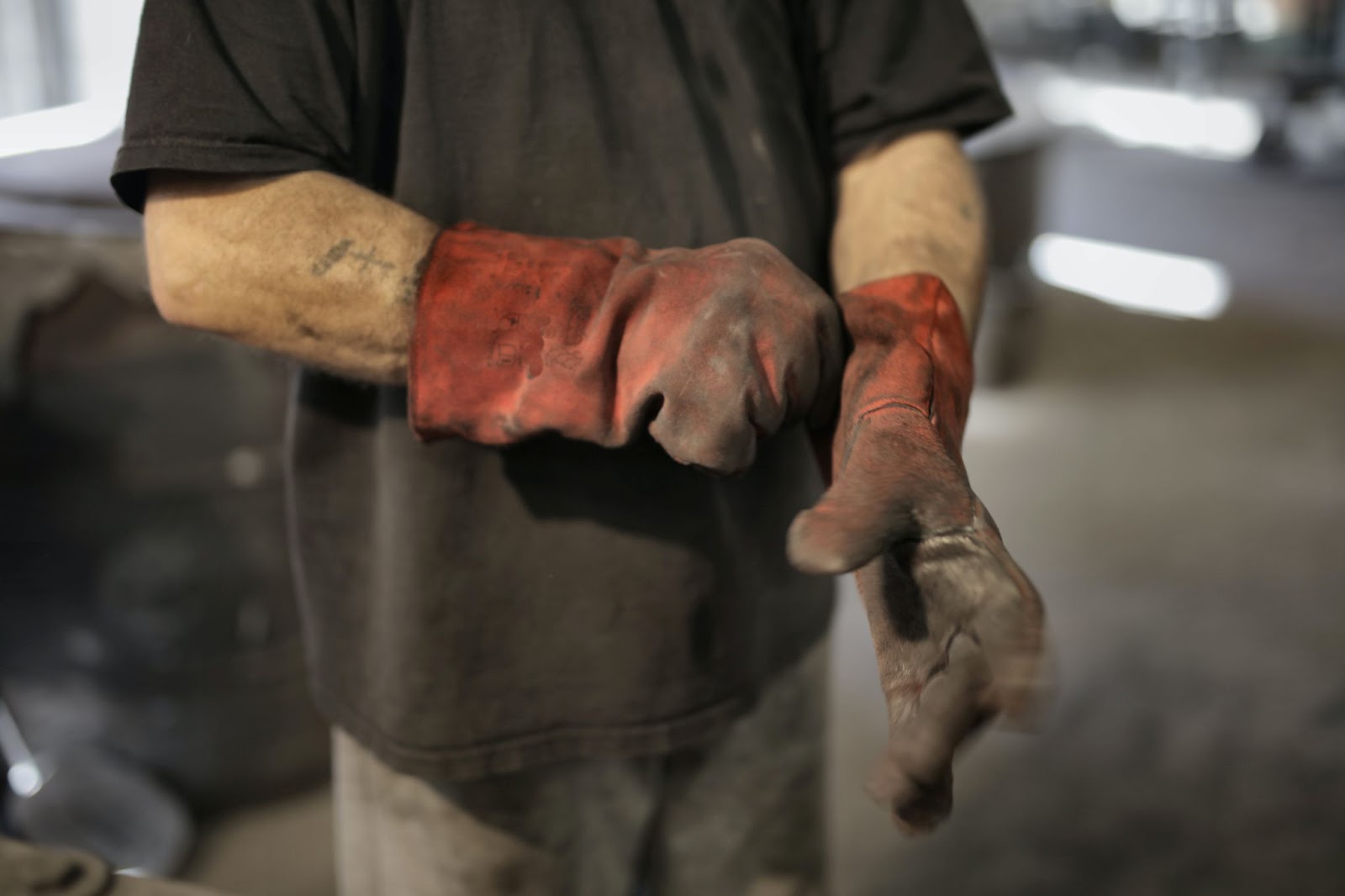
The construction process is meticulous in general. It has unique goals—and equally unique hurdles. The problems begin from the initial stages, right from the legal matters of land titles and acquisition which are not encountered in the other industries. The evident distance between the place of production and execution adds to the hurdles with real-time operational difficulties—the geo-physical factory limit is also high in large-scale projects, making the cost of the construction process soar high. On the other hand, manufacturing industry has a lesser limit that achieves cost efficiency along with better and timely communication.
Solution: The fatigue can be avoided by creating awareness about the common challenges.
The unsettling mindset of the workforce
The workforce in the construction industry is known for their adaptability and talent—but their lack of preparedness becomes the one thing that takes them down. When compared to the manufacturing professionals, they show a decreased problem-solving capacity that also affects the process, due to the resulting delays and cost constraints. This may also be due to their low individual performance occurring as a result of the disorganized workforce and working styles prevalent in the field. The changing roles in the system increase opportunities for the negligence of the employees both in terms of work efficiency and practice.
Solution: The workforce can be motivated to develop a positive approach towards the work system.
The variegations in the approaches
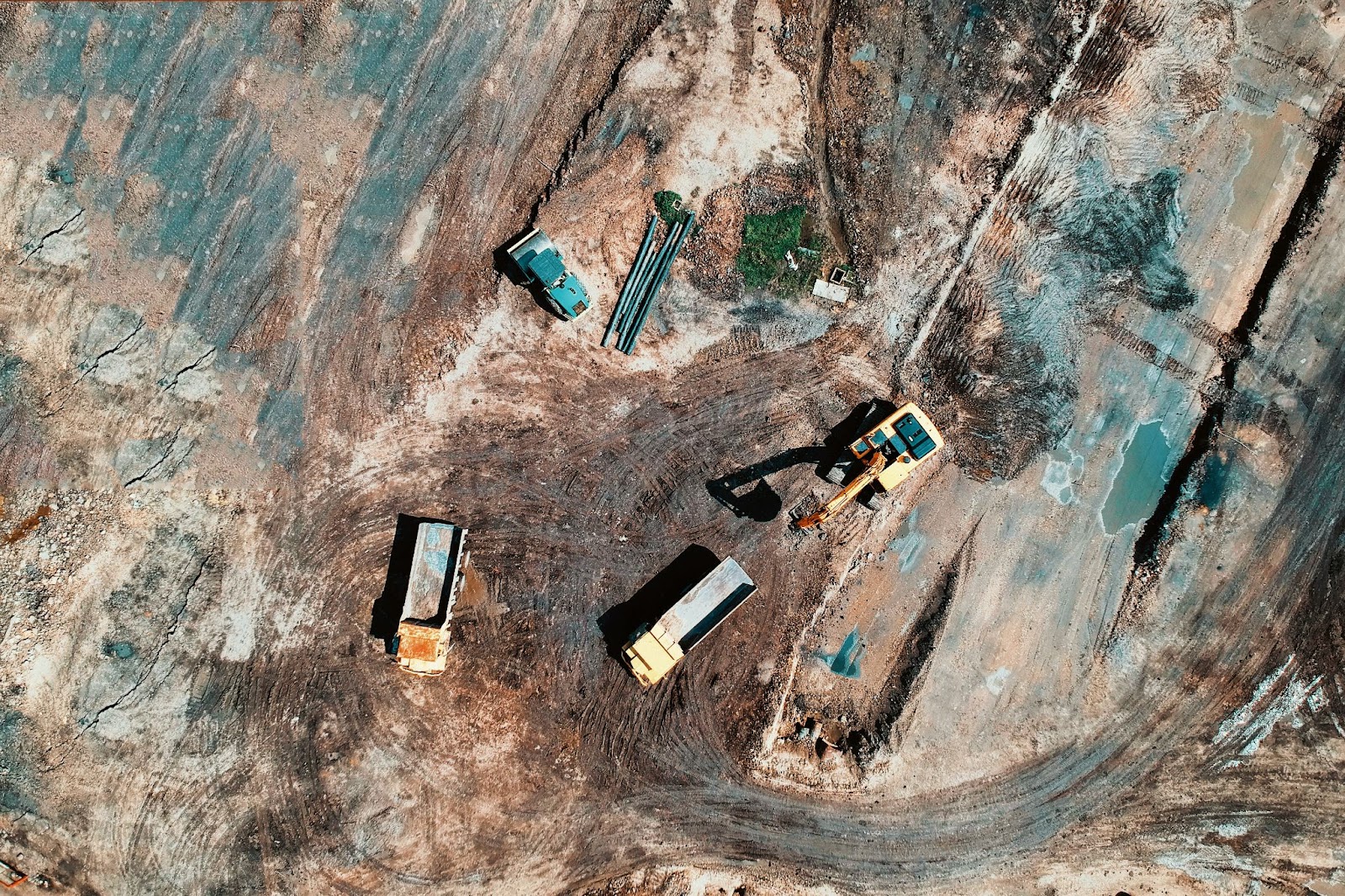
Unlike manufacturing industry, the construction industry is yet to achieve advancement in equipment, techniques and special training involved in incorporating the same. New revolution in customary practices is often questioned than being experimented with. There is also a considerable inadequacy for separate training facilities that makes it hard for the workforce to accustom to the new reformations at work.
Solution: Standard guidelines and protocols can be set while introducing new approaches.
The chaos behind the work structure
A field as extensive as construction demands better, well-organized patterns of work. The phase-by-phase execution in the field involves a number of teams which makes it hard to fall into an organized structure. With majority of the on-site workforce being illiterate, important studies such as time & motion study etc. get missed out and the process only gets difficult. In most cases, reviews are called for only when the project is set over a large scale or when a certain issue is encountered. This makes the identification of issues more difficult. The lack of analytical approaches in such cases affects the projects and the industry on the whole. In addition to this, the quality is also affected by the action plans that are typically non-mechanized—and hence with low degrees of precision—left at the hands of nothing but the potential of every individual in the labourforce.
Solution: Well-defined work structures, documented plans and automation techniques can be mandated.
The variable of time
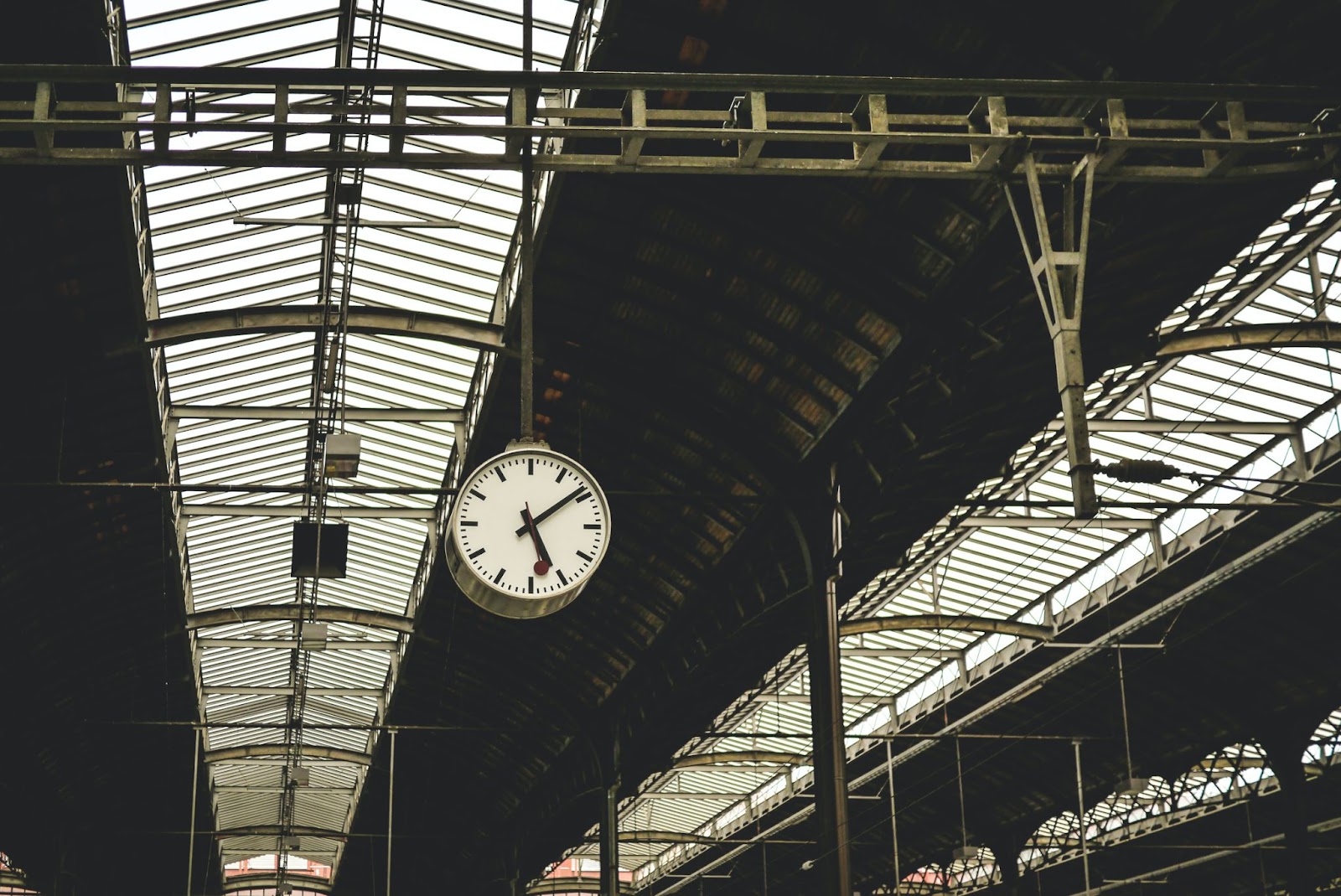
Time management plays an important role in everything from successful progress to the cost efficiency in a project. When it is not prioritized with stringent time schedules, time and cost overruns will slow down the project and leave the resources underutilized—or even exhausted. Although there are standard procedures to formulate the time schedules, it also needs to be revised for every new project according to its new process requirements—since it is unlike manufacturing industry where mass production is involved. With every next construction project, the cyclic process time for individual items can be the same but the variables increase and make the process far more complicated than they originally are, with lesser accuracy overall.
Solution: Digital tools specifically designed for quality control can be recommended.
The gap between revisions and conformities
In construction, it is important to know how to avoid construction mistakes. Because, in here, if identifying an issue is a problem, bringing a change is another. While random inspection and dependencies on visual checking give rise to the issues, the subject of change creates a more serious roadblock since multiple teams are involved. The vast workforce needs to communicate the changes and ensure an end-to-end solution that is approved in a methodical manner—much like the quality inspection protocols in manufacturing processes. The non-conformities to the changes may create a gap between the revisions and the end results, and affect the benchmark of a construction practice.
Solution: The quality can be quantified in standards for a planned control in case of a change.
Although the construction industry has been facing these issues, it has certainly answered all the concerns with better approaches, some of which have been adopted in comparison with the other fields. Systems like the pre-cast or pre-fabricated systems from the manufacturing sector have been tried and tested with in-site construction to decrease tolerance and enhance quality across a majority of modern-day projects. More adaptations are on the rise and the construction industry is soon expected to reach its previous glory.
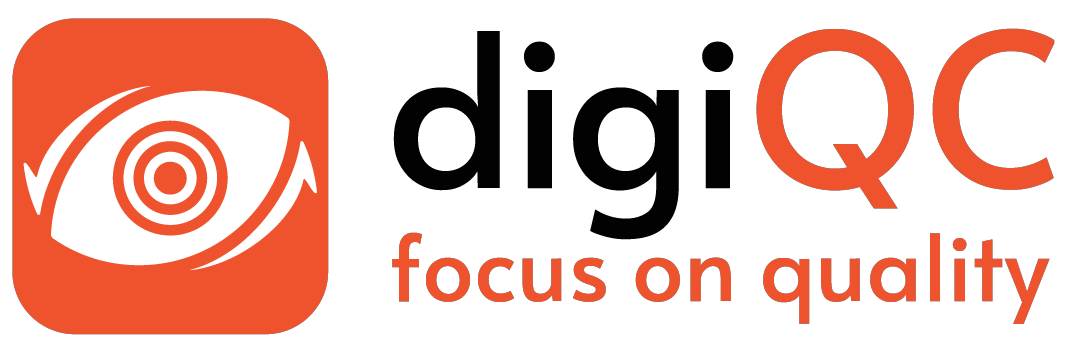
You can bring this change into effect right away if you use the cloud-based softwares like digiQC that simplify how you store, collect and retrieve your quality checks.
Read how digital technology is changing the construction industry to know more.
If you are a project owner, general contractor, trade contractor or a consultant looking to improve your construction quality, contact us now!
Need more particulars on the field of construction? Check out the blog: Construction industry—An Overview to find everything you need to know about the industry.