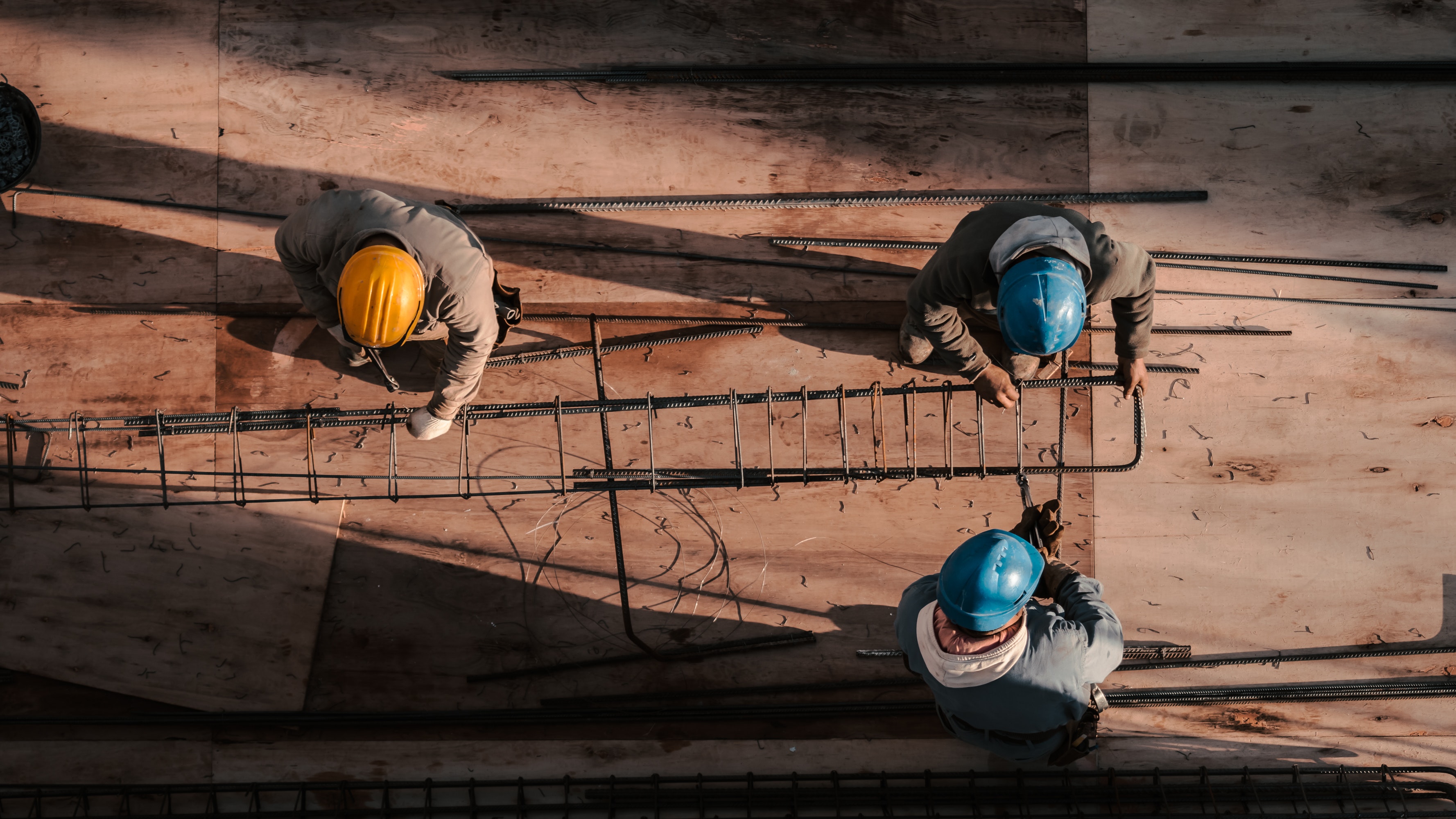
Being in the competitive field of construction demands a lot of efficiency in today’s date, given the swift progress across different parts of the field. The growing scale of the projects is also increasing the pressure on a project’s efficiency in terms of all parameters of construction:
- Time allocated for the project
- Cost of the project
- Quality output of the project
Among these, the project quality becomes a major concern since both time and cost factors are dependent on it. The assurance of this quality falls under the responsibility of a quality engineer who performs the quality checks based on an important document called an Inspection Test Plan (ITP).
Inspection Test Plans are:
- Plans for the work order/program of quality inspections
- Statistical test procedures with reliable results
- Multi-step processes with test points and verification protocols
These ITPs are crucial to a quality assurance program—and hence, are carried out before, during and after the project realization process. But do you know why it is so important for quality management?
Read ahead and understand why Inspection Test Plans are critical for your construction business.
If you are running out of time, connect with our team and discuss the pros of Inspection Test Plans (ITPs) for your next project.
Inspection Test Plans meet the quality standards in ISO 90018
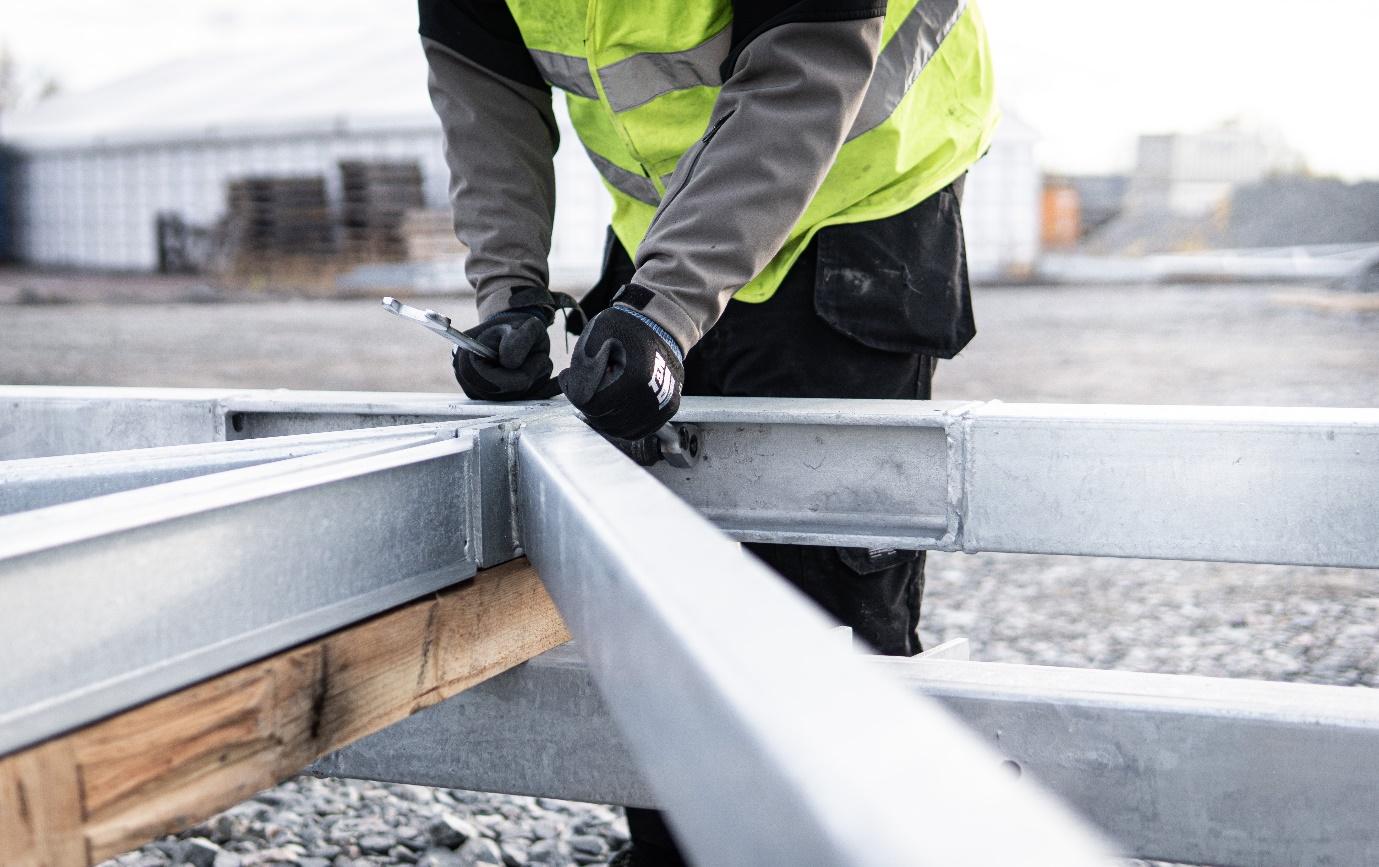
Over the years, the field of construction has undergone a strong evolution that has created a need for exercising construction standards across both work and practice. The ISO 90018 standards establish quality control for products and services through ITP mandates that include verification of material, product and service conformance. It also calls for a test plan that is carried out across every appropriate stage of the project and verified to be in the acceptable criteria, by a suitable professional in charge of the particular work or item.
Inspection Test Plans prevent cost overruns on your project
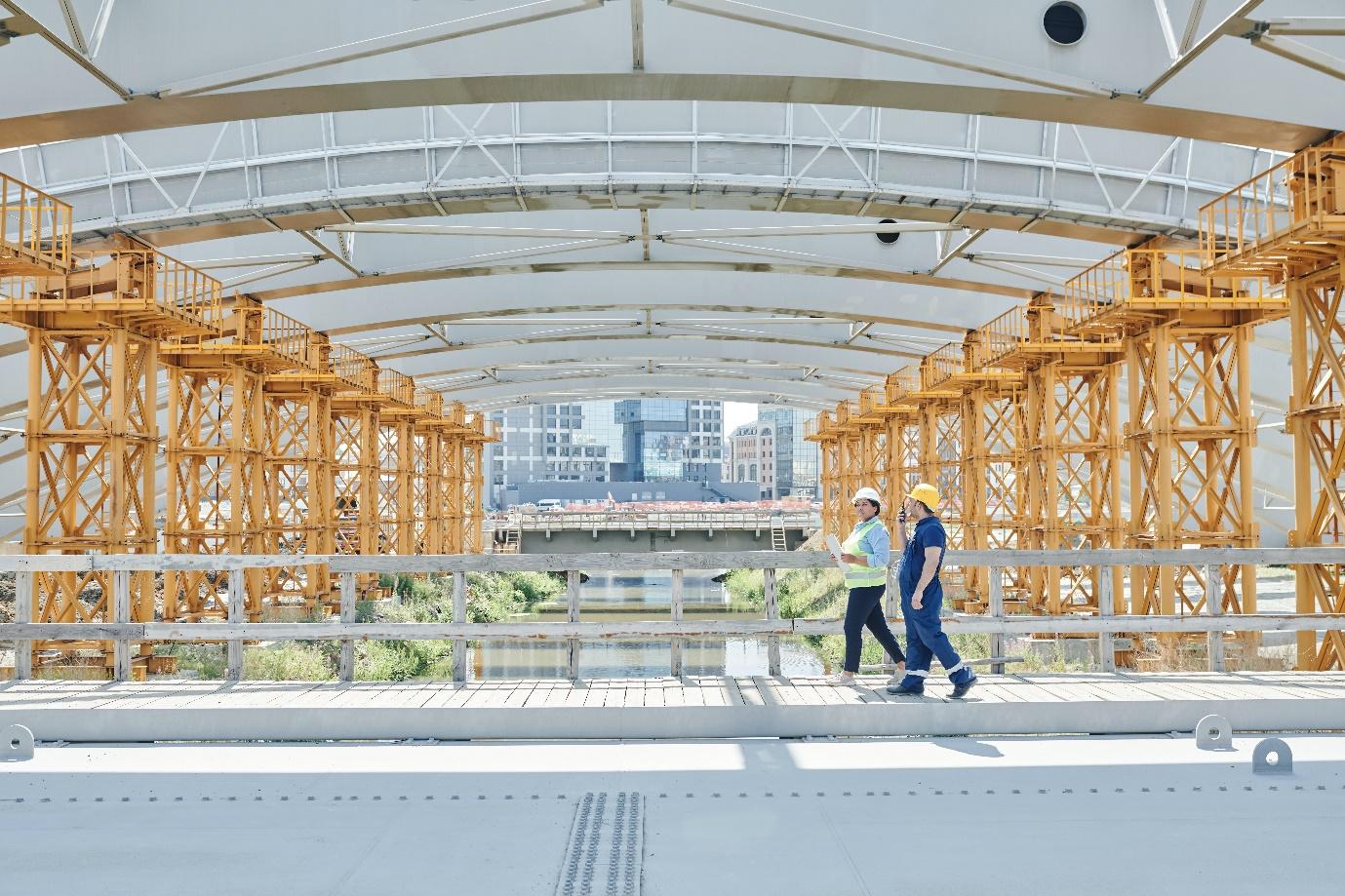
The cost of a project is one of the indicators of the project’s performance, due to which it is given importance with stringent quality management. Such costs may differ from the budget only in three cases:
1. If the cost is spent on low-quality materials/activities
2. If there are any delays/deviations from the plan of work
3. If there is a case of risk or rework requirement due to defects
With a clearly documented plan, the Inspection Test Plans (ITPs) shall identify risks and quality defects on time and prevent delays in the project that may give rise to extended storage costs, extended bond costs, material inflation costs and other indirect costs that may arise both on-site and off-site.
Inspection Test Plans keep the project schedules on check
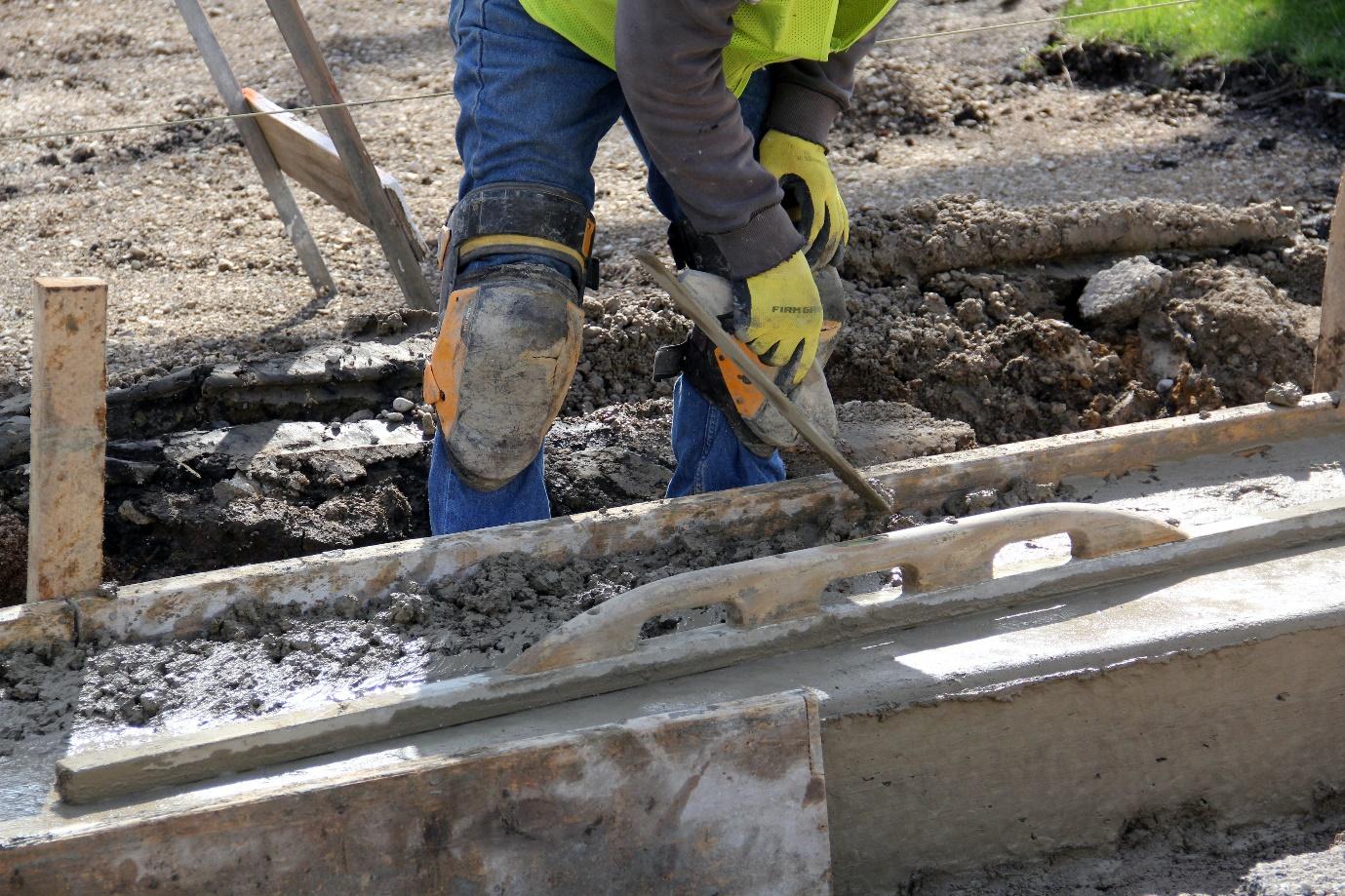
Delayed projects are as disappointing to the construction team, as it is to the client. To avoid delays, it is recommended that a project has a work breakdown structure where multiple Inspection and Test Plans are scheduled. These plans can help in monitoring the compliance of the work/item to the quality requirements and help it proceed to the next stage seamlessly. By working on the test stage and frequency of these plans, a project can be assured an on-time completion with maximum quality compliance. This will prevent reporting of issues with:
- Performing a required set of inspection procedures with a set time
- Ordering of materials/supplies
- Renting of equipment and labour
- Allotment of work and responsibilities to sub-contractors or teams, among others that will be affected by non-compliance with time.
Inspection Test Plans give a direction to multiple teams
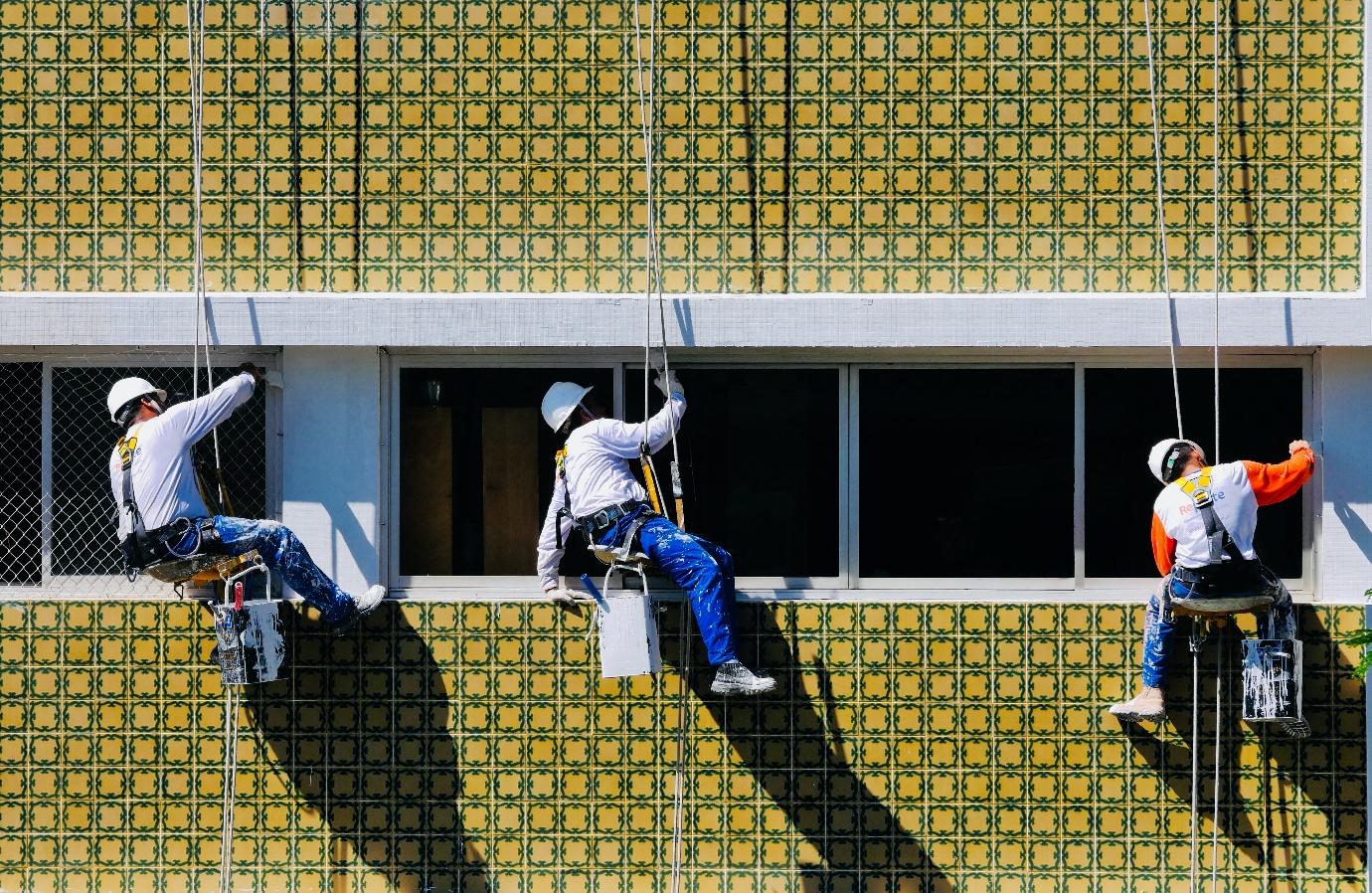
Inspection Test Plans have a clear sequence of work that gives specific assignments and responsibilities to different parties. This is standardized with a set of criteria that satisfy the quality requirements in a well-documented process. A standard inspection criteria process includes:
- Surveillance (S)
- Execution (E)
- Witness(W)
- Hold Point (H)
- Review (R), and
- Records (RE)
These are verified by quality control teams as a checklist or a standard document which serves as a reference across different stages of a project—and shall be monitored and verified on the whole in a final inspection, prior to the final completion of the project.
Digital Inspection Test Plans simplify the collaborative actions of teams
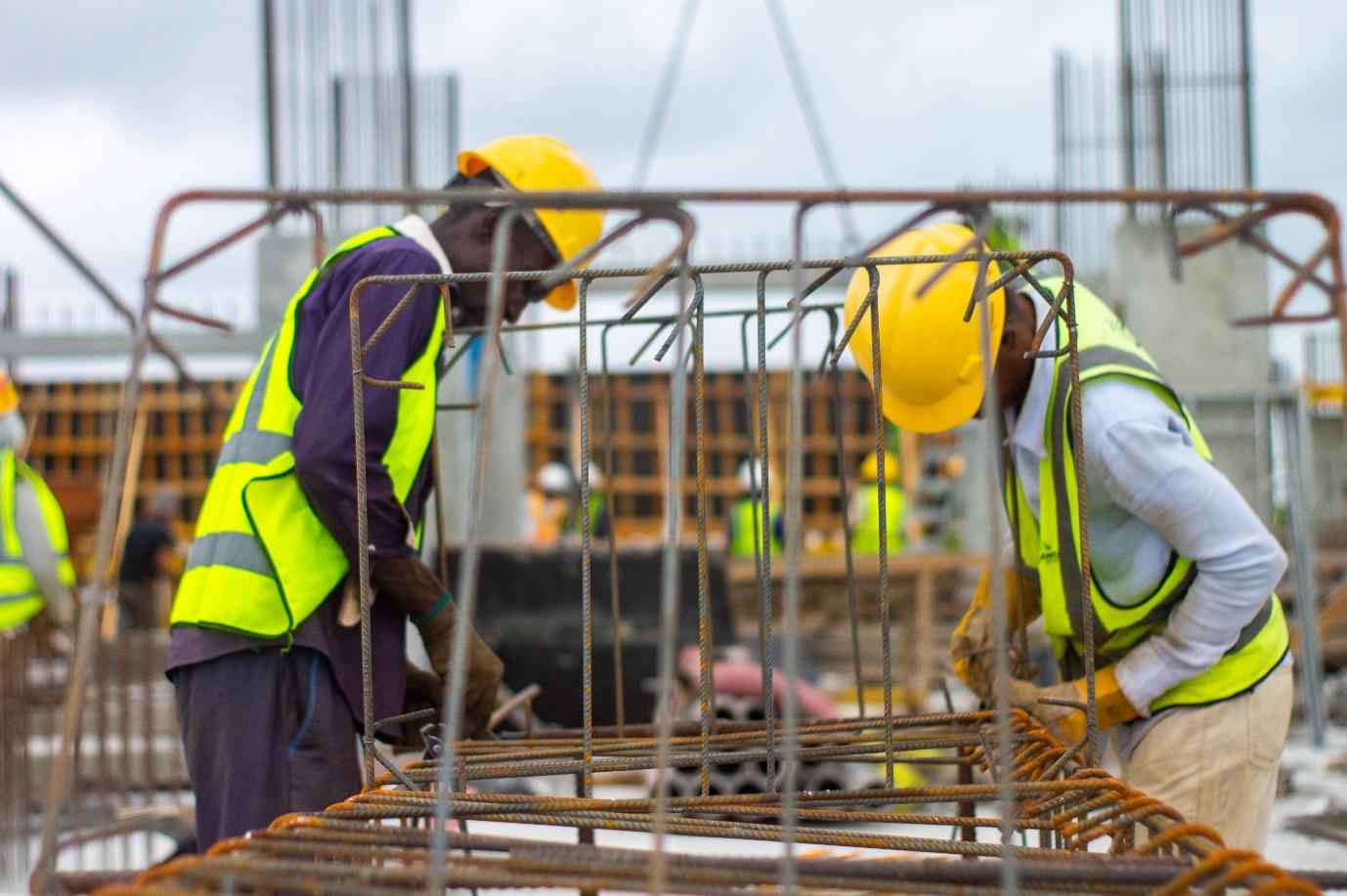
Due to the complexity and ambiguity of manual Inspection Test Plans, modern construction businesses have started using digital tools that simplify the entire quality management process. Given the multiple teams in a construction projects, especially in the large-scale metropolitan projects, the digital platforms are preferred the most due to:
- Easy customisation according to the team’s expertise and project requirements
- Quickly shareable reports with comments and action points for different teams
- Instant verification by multiple professionals in both on-site and off-site teams through mobile channels
- Better end-to-end quality management with overall analytics and other useful features
Take 20 minutes of your time to read more about quality management before getting started. Get a quick heads up with this blog: Quality management in construction—An Overview
Are you eager to know how to create an Inspection and Test plan digitally? Reach out to the quality experts at digiQC and get A-Z of quality management done for your project in a smart, digitized system.
digiQC is a cloud-based quality management software that inspects on-site work in real-time. It simplifies how you collect, store and retrieve your construction quality checks.
.png)