Did you know that statistical analysis shows that on average a construction worker 40 hours a week works an average of 10-12 hours a week of overtime! Still, the slowest growth noted is in the construction industry. The reason behind this is a reduction in productivity rates of the construction industry.
Although contributing 5% to the nation's GDP, the Indian construction industry has the slowest growth rate of any other sector in India. This growth rate has been slowly increasing over the last three decades but has faced setbacks due to the global pandemic.
The reason behind this is many but one of the most critical factors is the minimal use of digital technologies on construction projects. The global pandemic boosted the use of digital technologies in the Indian construction industry. So let us see how construction productivity has increased with the use of digital technology.
How is productivity calculated?
Productivity is calculated in terms of total work executed with respect to n.. of workers and average hours of work.
Productivity = Total output / Total work hours
= Total Output / (No. of labors*Average work hours)
Construction productivity is generally in cubic meter/man-hour for concrete, kilograms/ man-hour for reinforcement steel, and square meters/man-hour for masonry, plaster, and tiling work.
The construction productivity calculates the time spent in getting prints, delays due to processing of a request of information, time spent on inspections, and time spent on rework and rescheduling. Let's see how productivity and efficiency are reduced due to some concerning factors.
Reasons why productivity and efficiency are decreased on construction site
As we discussed earlier, man-hours considered in productivity include a wide range of factors. Some of them are listed down below:
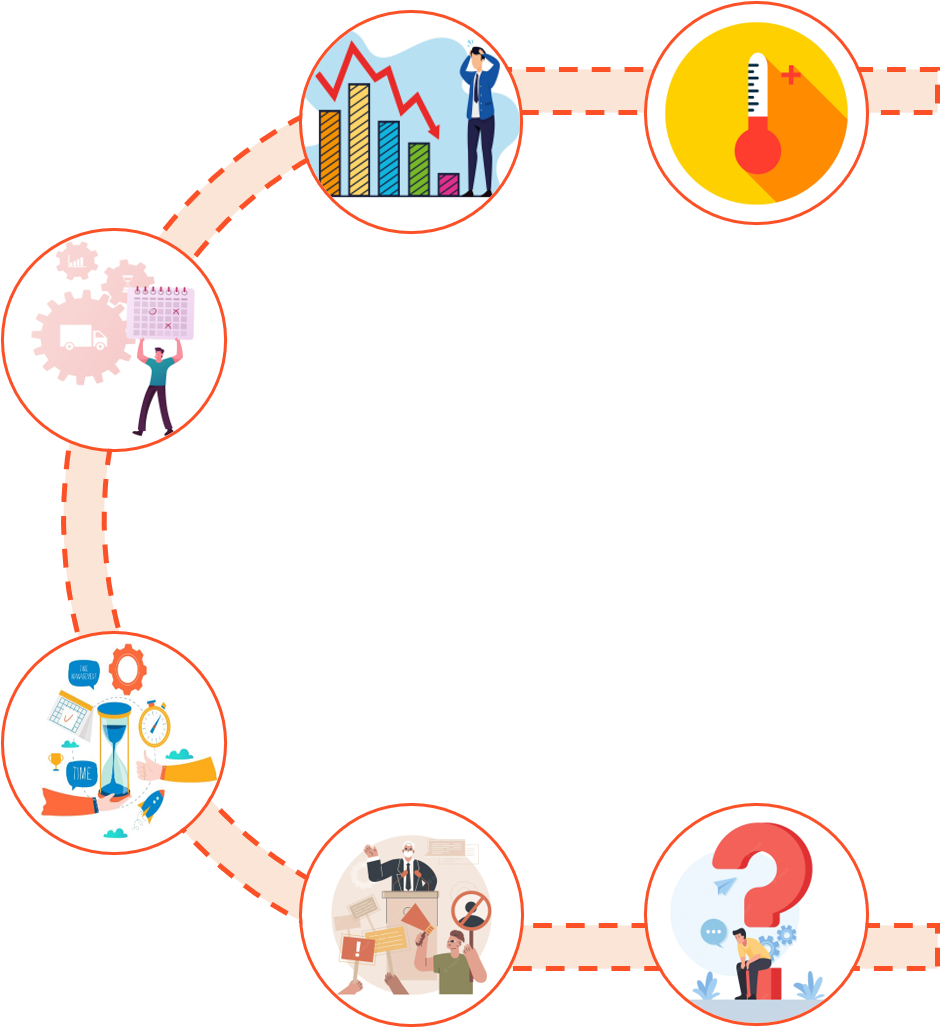
- Weather Conditions
India has a hot and humid climate. Working in very hot weather has both psychological and physiological effects. Psychological effects include restlessness, irritability, and an unenthusiastic approach toward work. The physiological effect includes heat stroke and heat exhaustion.
This is conditions also affect site professionals. They get tired of doing paperwork due to outside temperatures and sometimes they fill in phony results on the checklist. Given the conditions, we cannot blame them.
- Market Conditions -
The material shortage is one of the most for reduced productivity. Market fluctuations lead to inflation in prices and that, in turn, makes materials less available to all the customers.
Secondary to all this, if the material is ordered and there is no place to store them on-site, it would create a site logistics issue. Even if there is some sort of storage available, dumping material in an inappropriate place would again require laborers to transport them to the desired location. This extra labor would contribute to reduced productivity.
- Design and Procurement
During the design phase, changes are inevitable. But changes during the procurement and execution phase cast cost management money as well as time. This leads to confusion, rework, and frustration among the workforce.
- Construction Management
There are many subtexts to this. But the major subtext is described below.
- Ineffective Communication: Ineffective communication leads to disruption of the supply chain, wrong material orders, and wrong execution.
- Inadequate Planning and Scheduling: Construction management initiatives always lead to a positive work environment and promote productivity. While the opposite, just creates chaos, rework, and reduces enthusiasm.
- Government Policy
Government statutory approvals are an inevitable part of a construction project. Though the process to obtain them is tedious and can affect the timeline of a construction project as a whole.
- Lack of Training
Statistical analysis shows that when workers are properly trained and given the knowledge they contribute to efficient working. But traditional practices don't encourage such practices due to a lack of resources.
Remedies to mitigate the problem
We have already established that promoting digital technologies on construction projects helps boost construction productivity.
Let us understand how digital technologies help. First and foremost we need to understand a little bit about digiQC and how it functions.
digiQC has a web module for stakeholders and a mobile app for site personnel. In this modern world, everyone uses a smartphone and digiQC is one click away!
Web modules help stakeholders in assigning tasks and site personnel can complete the requirements using the digiQC app. Using the digiQC instructions app, site personnel can also raise queries involving multiple agencies and stakeholders.
However, the question arises as to how it helps in increasing the productivity and efficiency of the users. Let's check the comparison given below on how digital technology increase productivity on site:
- Weather Conditions:
Conventional - Consumes time for inspection.
Digital - As we discussed earlier weather condition affects both the physical and mental capacity of workers as well as site professionals. With digiQC a site professional has to spend less time filling the checklist in harsh weather conditions.
- Market Conditions
Conventional - Does not promote tracking and invoice generation which tend to get lost.
Digital - Notifies the activity checklist to be filled in prior. This gives time for prerequisite materials to be arranged in advance. The site planning needs to be done by the management consultancies to avoid any miscalculations.
- Design and Procurement
Conventional - Takes time to transfer the changes from the higher level of the workforce to execution personnel. Also, the design idea comes via a channel of multiple people which has a high frequency of misunderstanding the idea and inserting changes that were not added earlier.
Digital - The design ideas are directly shared with the workforce on a central level. This helps in promoting transparency as well as execution personnel feel valued for their input. This promotes a positive work environment and which in turn directly promotes increased productivity.
- Construction Management
Conventional - Has ineffective communication techniques and any communication is not documented for later problem solving as well as management initiatives lack coordination and planning.
Digital - with digiQC you can plan your workflow as well as document all the communication through the digiQC instructions app.
- Lack of Training
Conventional - Lack of resources does not promote proper training of site personnel and doesn't allow them to learn and adopt new technologies easily.
Digital - With digiQC, you can transfer your quality control completely to digital mode. This helps in saving time as well as motivates them towards more technological advancement.
Essence of the blog
The conclusion that can be drawn from this blog post is that there are many ways in which digital technology such as digiQC provides the upper hand to construction professionals. They help them grow and transform their business capacity and help in the advancement of the whole industry.
Critical factors affecting construction productivity can be counteracted with help of digital technologies will increase productivity and efficiency of construction workers.
You can find us on LinkedIn and visit our website. Use the digiQC instruction app to collaborate and raise queries or issues!
Would you like to know more about Digitization in Construction? Head straight to the blog Digitization in construction—An Overview to know how you can achieve high quality and performance in your projects.