Doesn’t perfect quality requires a lot of effort from the management team? It requires timely management of multiple resources that are transmitted via a large number of people in the same or different organizations. This generates demand for upholding the new market trends that ease these processes and aid in achieving predetermined goals to fulfill clients’ expectations. Now let us first understand how the PDCA cycle for quality management was developed and what are the multiple resources used to support this cycle.
PDCA Cycle was first developed by a management consultant Dr. William Edward Demings in the 1950’s. It is also popularly known as Deming’s cycle. This model helps in building a continuous loop for controlling & improving processes. It is a very basic model which makes it more accessible in the Indian construction industry that is in the revolutionary phase of project management systems.
This approach divides the processes into simple basic steps. It helps in improving processes in-country and eliminating repeating errors. This is a stand-alone method but is also adopted in lean methodology as a valued tool.
Principles of PDCA Cycle
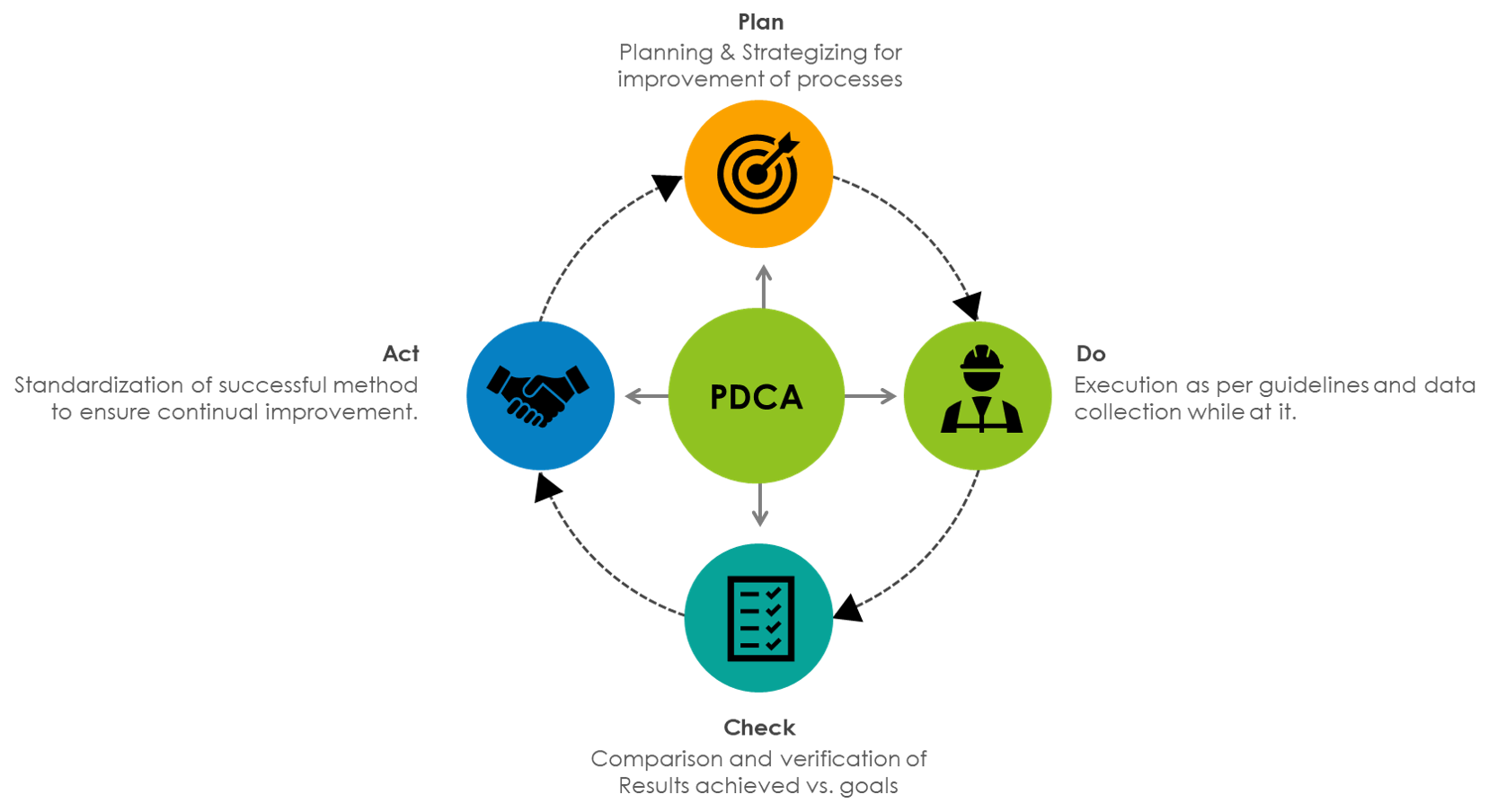
Plan
This is an input stage of the cycle. It identifies the problem, planning and strategizing a series of events to mitigate the risk. Points taken into consideration at this phase are :
- Which is a repeating error
- The root cause of a problem
- Solution strategy of required problem
- Resources required for a problem
- Budget required for planned strategy
The planning stage is further subdivided into 4 stages:
1. Identification of repeating error: It is analyzing stages on basis of results obtained and general observation across the site.
2. Detailed Investigation: Retrieving information and deploying tools for investigating the problem such as a basic reconnaissance survey or execution of activity in front of a subject expert.
3. Finding Root Cause: Analyzing all the details extracted in the earlier phase and analyzing through management tools such as cause and effect diagrams and what-ifs? tool.
4. Summary of the plan: Strategize a plan for improvement. Plans need an implementation strategy that can be initiated in a small but significant stage.
For example, all the quality processes are defined in the planning stage along with the authority matrix of work. This shall include who is authorized to do which type of quality control and at what frequencies. It also includes checklists to be followed for the construction work.
Do:
This is the execution phase. It requires the appointed person to execute the task as per the direction given. It requires precision as these small steps results will affect the overall performance of the task. Simultaneous tasks executed along with implementation are quality control, minute detailing, and observation. This works as input for the next stage. Data collection is done to analyze it further. This is both the output and input phase.
Based on the planning done, execution and quality control are done. These reports are stored and can be later used for analysis purposes.
Check:
The input data from the previous stage is sorted, organized, and analyzed here. Analytical tools are introduced to find any point of correction in a previously known impeccable plan. The strategy has a successful outcome and can be implemented on a large scale if not found.
The key feature of this stage is the comparison of achieved results to outlined expectations. Comparison can be done in terms of quality achieved, Time taken, resources wasted, a margin of error received and percentage of error eliminated.
At regular intervals, the quality data and the process followed are reviewed. Root cause analysis and trend reports are generated to identify the cause of the problem.
Act:
It is a standardization of successful strategy. For a successful strategy, resources that are required for implementation are calculated. The process of acquiring and budgeting are the factors considered in the next step. That means if a strategy is successful in execution and delivers promised outcomes, but is very costly to execute. The decision depends on the client, whether or not he is ready to invest the sum of money for better delivery. If not the stage is used to authorize the dismissal for the same.
Based on the root cause analysis and available data, decision-making is done and necessary changes are made. Also, the training needs can be identified for the engineers and the contractors.
Different ways to Implement PDCA Cycle
PDCA cycle is a standalone development technology that is versatile and can be applied to a wide range of problem-solving statements. PDCA Cycle can work as the key to enhancing the quality management system but it has to be determined for which application it is being used. It is necessary to define this to draw the path of future processes and execution systems.
Some of the following applications are mentioned below:
- For evaluation of multiple viable solutions to a problem
- For the Development of improved design and better quality
- Implementation of new change
- Improvement of Existing Procedures and introduce new technology
- Continual Improvement Strategy of a prestigious organization
- Analytical tool in lean methodology
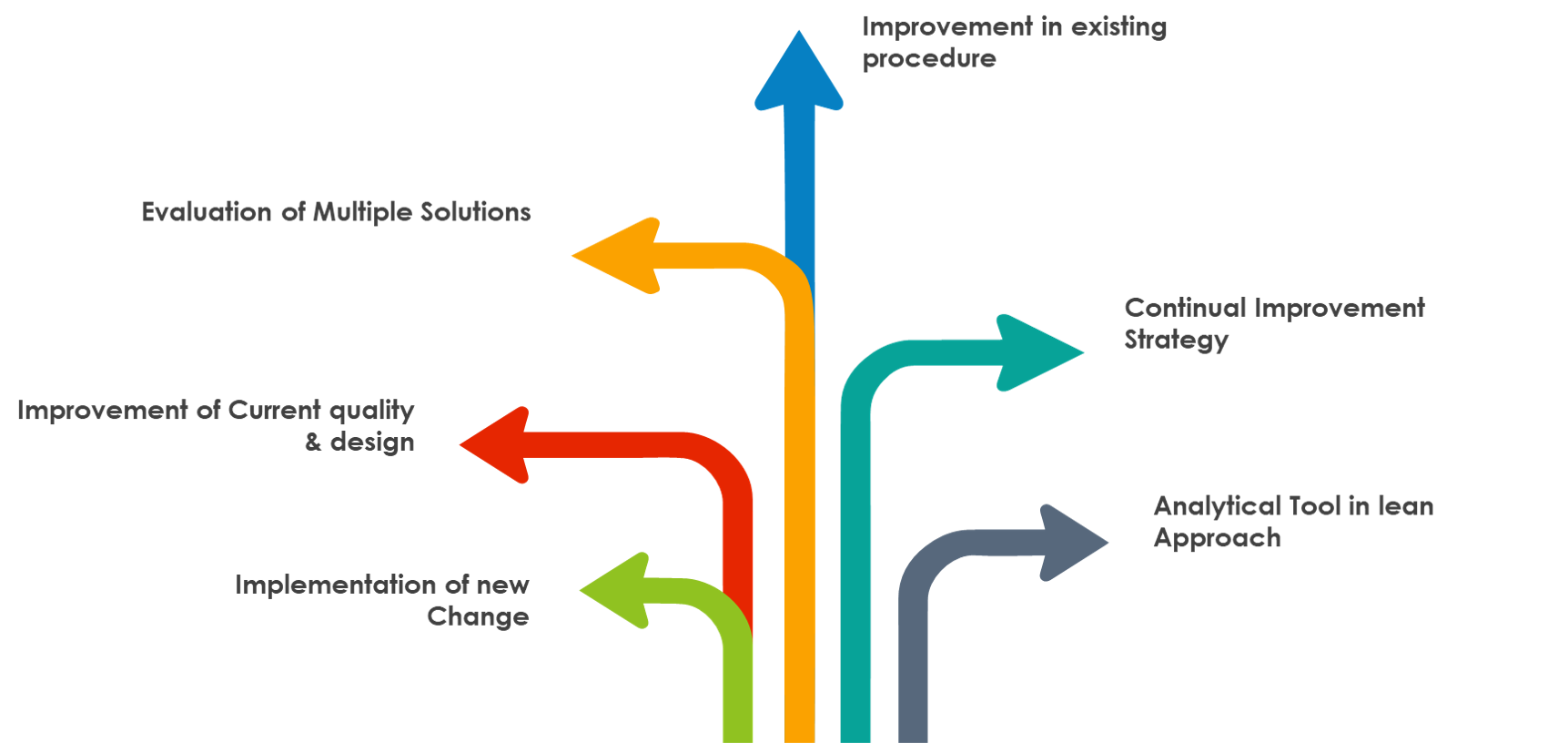
Advantages of PDCA Cycle:
Advantages PDCA Cycle is as follows:
1. Its value as a simple standard-setting tool cannot be undermined. It has the simplest model with basic steps that can be used to achieve the same results as other high-standard methodologies.
2. It prevents the repetition of mistakes and also promotes continual improvement. This method defines the strategic goals and defines improvement in stages.
3. Cost reduction due to elimination of wastage.
4. Increase in collaboration between central and site teams.
5. Increases reliability of strategy that is to be implemented in the field as it has achieved desirable success on a small scale basis.
6. Increased potential of mitigating risk before it happens on a large scale.
7. Increased efficiency and productivity promote a healthier work environment and growth
8. Decreases budget timeline by forecasting risk of failure in advance and has quick reaction time.
9. Drawbacks of PDCA Cycle:
Drawbacks of the PDCA Cycle are as follows
1. Continuously changing the status of activities due to improvement processes can be confusing and may deliver wrong results.
2. PDCA Cycle works best when conditions are ideal and the action starts with the planning stage. It doesn’t give instant solutions and contingencies.
3. Over-analysis is common in the PDCA Cycle as the execution stage has no input criteria.
4. Slow improvement sometimes adversely affects the work environment.
Conclusion
There are always negative and positive sides to a thing. But there is always scope for improvement for reducing disadvantages. PDCA cycle can be adapted for a wide range of construction organizations i.e from small-scale companies to large-scale organizations. PDCA Cycle has a very basic model which makes it easily accessible. Thus, one can Adopt the PDCA cycle for a wide variety of applications in the construction industry and can ensure quality control is enhanced.
Here we conclude cases of high quality management approaches used by construction industry individuals. We discussed four high-quality management approaches and detailed the principles involving each approach. Any of these approaches can be adopted by construction industry individuals to provide superior quality for customer satisfaction.
Are you eager to make your customer happy with good quality management? Read the in-depth blog series from digiQC: Quality management in construction—An Overview to know how!